塑橡膠成形機台於模具之加熱一般採用電阻式和熱媒式之加熱方式,這兩種方式之能源使用效率不高,而新的加熱方式為「感應式加熱技術」,其原理為利用交變磁場於模具上產生渦電流來加熱,此種加熱方式之能源使用效率高,能節省能源,本文介紹用於感應式料管與模具加熱技術。由於感應線圈的幾何樣式對於加熱場形影響很大,本文針對料管設計三款樣式感應線圈為例,分別以多物理量耦合軟體進行電磁熱分析,結果顯示最佳線圈樣式之軸向溫度分布數據為:最大溫度為211.64℃、最小溫度為160.49℃、平均溫度為190.61℃與平均溫升為160.61℃。而徑向溫度分布數據為:最大溫度為194.91℃、最小溫度為186.39℃、平均溫度為191.96℃與平均溫升為161.96℃,線圈的能源效率為83.43%,後續介紹感應加熱主機之電力逆變模組裝置,應用於負載諧振感應加熱系統之上,於全橋式逆變器電路架構下,利用功率變壓器的電感搭配感應加熱線圈與諧振電容產生共振,進而使功率開關上的切換能量獲得適當的轉換。傳統料管的加熱方式,以電熱片加熱廣為業界使用,但電熱片加熱速度慢、能量傳遞易散失、加熱溫度不高等多數缺點。為此,PMC開發料管感應加熱技術與模具感應加熱技術,希望透過電磁熱轉換直接加熱料管與模具表面,可大幅縮短加熱時間與提升加熱極限溫度,且使能源使用效率提高並節省能源。
關鍵詞:感應加熱、料管、模具、電力逆變器
▋ 前言
塑橡膠成形製程屬於週期性生產模式(反覆加熱與冷卻動作),熱量在材料塑化階段、熔膠充填階段、熱反應固化階段時需求最大。製程中加熱能耗成本佔其整體生產成本比例偏高(熱壓成形製程加熱能耗占整體能耗92~95%;射出成形製程加熱能耗占整體能耗50%)。近年來功能性塑膠製品的應用與日俱增,如高表面光澤度、微結構塑膠製品、工程塑橡膠製品、複合材塑橡膠製品等,帶動高溫成形製程技術需求急遽擴大。在熱壓成形製程中,提供高效快速加熱技術,與高穩定溫度控制精度,可達到節省更多能源的目的;而射出成形製程技術需要將模具、料管溫度提高,以提升熔膠在模內及料管中的流動性、可減緩熔膠在模具表面成形固化層、或在料管、模具中卡料等情形,而這些製程需求,皆須使用高溫成形製程技術才能達成。感應式加熱製程技術為高溫成形製程技術之一,國內學界研究與國外揭露文獻顯示,感應式加熱製程技術相較於傳統電熱式或熱媒式加熱製程技術,具有9 倍加熱速度、1.6倍能源效率及提高產能效率2.6倍的優勢,能耗為蒸汽式1/2~1/3,電氣式1/5~1/10,亦為國際技術趨勢逐漸聚焦感應式加熱製程技術之主因。
研究背景與動機
國際節能議題政策以歐盟等國家為主要發起國,如巴黎與德國對於改善全球氣候暖化及提倡綠能、零碳排之議題十分積極,無論是法規制定或是相關節能技術研發皆領先全球其它地區,國際重大協議又以2016年生效的「巴黎協議」與2019年發布的「歐洲綠色新政」為國際標竿,內容提到未來能源生產和使用須優先考慮能源效率,並揭示2050年要達到碳中和,2030年減碳50%~55%之目標。
依據新能源政策之推動,經濟部能源局編撰「2016年能源產業技術白皮書」以推動各項能源技術研發及推廣應用成果為主。其中技術研發重點分別為新式及再生能源領域技術研發,以及節約能源領域所屬次領域,包括工業節能、住商節能、跨部門節能、智慧電網等項目,投入國家資源進行技術研發與相關節能成果推動,故PMC投入產業省能技術之發展,推動料管與模具感應加熱,並擴展至橡塑膠節能技術,以達到產業節能減碳之目的。
▋ 料管電磁熱耦合分析
電磁熱耦合分析是利用有限元素的集合離散架構,分析實體電磁感應線圈的幾何模型,每一個元素代表這個實際架構的一個離散部份。元素和元素中間存在著共用節點來連接,節點和元素的集合稱為網格。在一個區域的網格中存在的元素數目稱為網格密度,每個元素均遵守物理基本理論方程式(ANSYS,1995)。根據物理場域,介質特性及Maxwell理論,導出電磁問題統御方程式,後續代入熱力與熱流理論方程,並利用餘數加權法對微分形式的統御方程式進行離散化,導出一個具有龐大的稀疏對稱矩陣之代數方程組(Davies,1990)。利用此法,將感應加熱主機實際輸出之條件作為模擬分析之邊界2條件,進行電/磁/熱耦合分析。
模擬流程
本研究利用有限元素軟體COMSOL 軟體進行模擬分析演算過程可分為電磁耦合分析及磁熱耦合分析,其模擬流程如圖一所示。
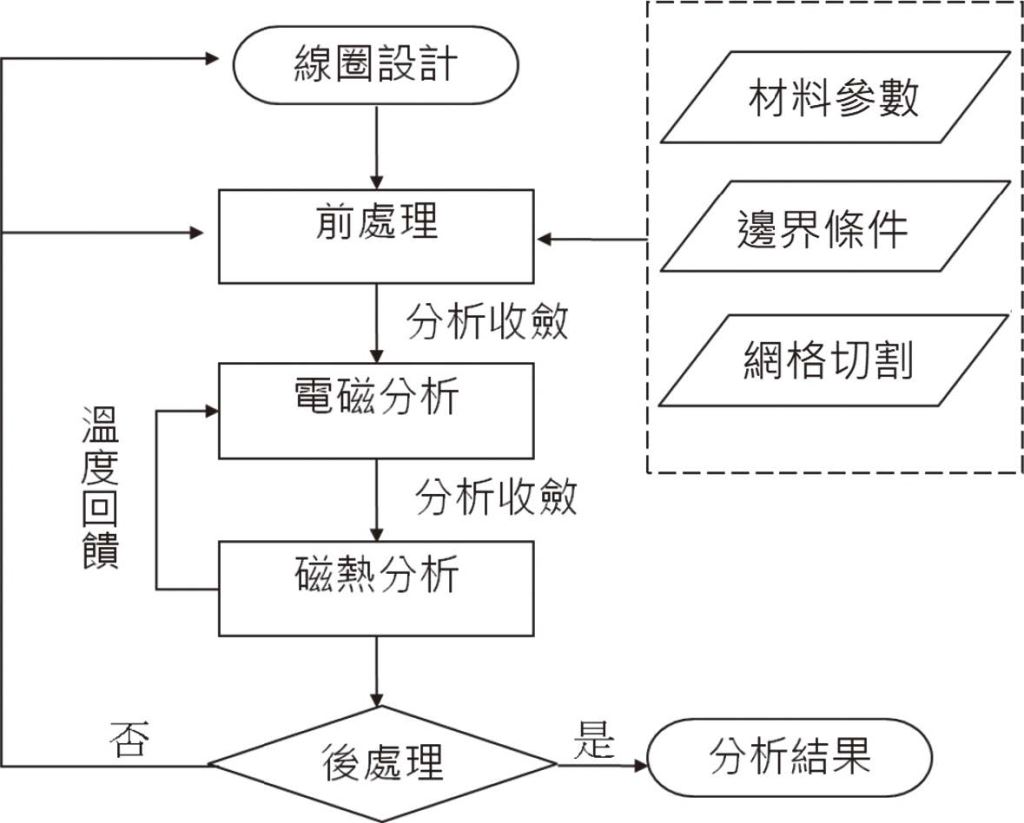
圖一、模擬流程
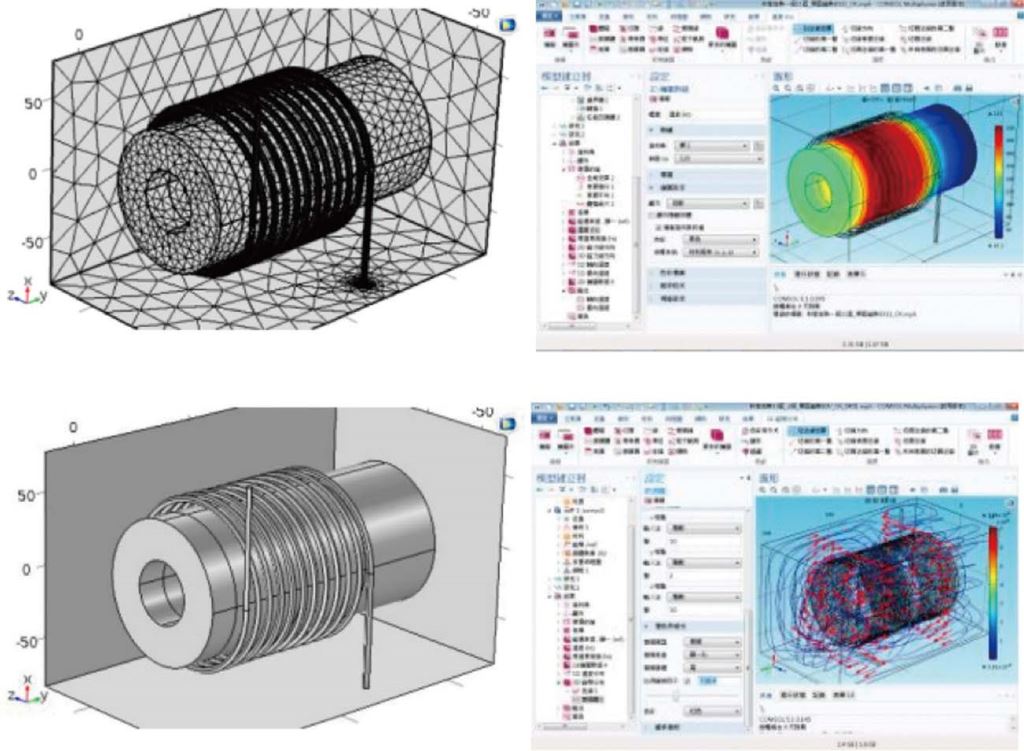
圖二、有限元素分析軟體介面
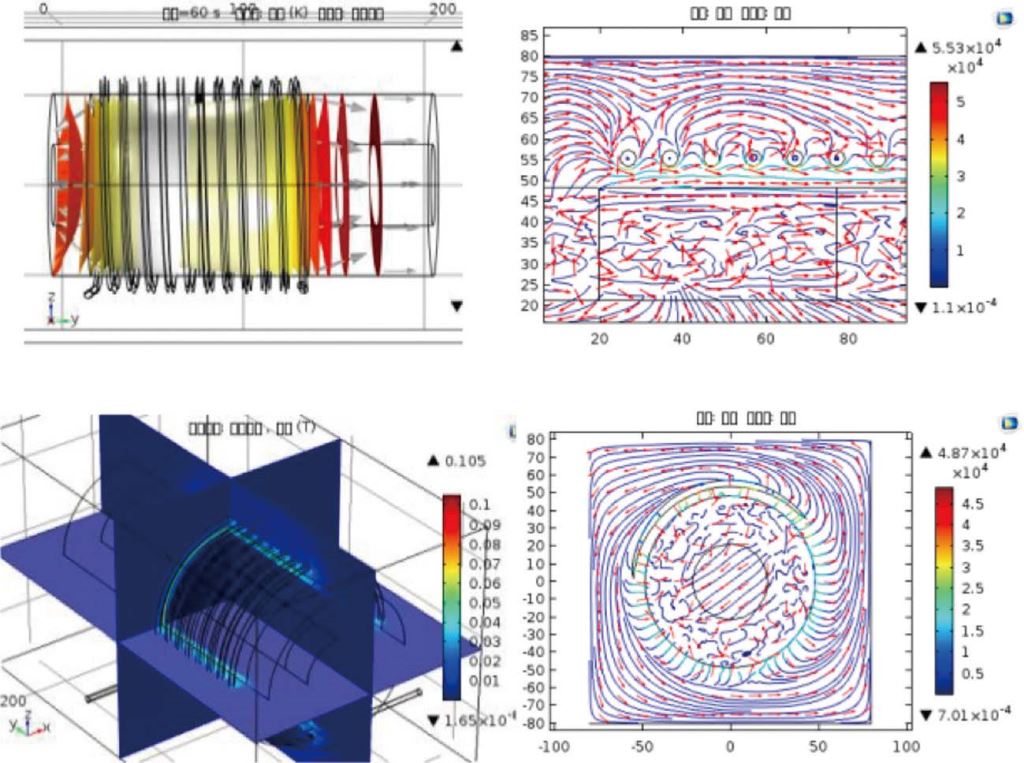
圖三、電磁熱耦合分析模擬介面
線圈樣式配置
- 線圈設計:針對現有料管規格或結構尺寸,依電磁加熱原理,設計出線圈樣式,並進行模擬。
- 前處理:分別須進行材料參數設定、邊界條件設定及網格建立。依據實際使用材料,將參數設定於軟體中,或直接尋找軟體內建雷同之材料,按照感應加熱主機之輸出參數設定為邊界條件,以模擬出較符合實際情況之結果。而網格劃分多寡影響計算結果及收斂性,網格數量多且密,有助於提高結果之準確性及收斂性,但卻易於影響計算時間,故建立網格時需多注意網格大小及分布性。
- 電磁分析:屬AC/DC 之分析模態,以電流、電壓為初始邊界,計算出磁場強度與磁場分布。
- 磁熱分析:將電磁分析結果進行固體熱傳分析,考慮熱對導磁係數之影響,可將熱傳計算結果,回傳至電磁分析重新計算。
- 後處理:依據顏色分布圖、流線、箭頭等方式呈現電磁及磁熱之分析結果,針對線圈設計不良處予以改良,並重新計算直至達到預期加熱效果,有限元素分析軟體介面如圖二所示,電磁熱耦合分析模擬介面如圖三所示。
- 若要將射出機料管感應加熱,感應線圈樣式設計的結果,直接影響加熱場形與效率。本文線圈依據電磁熱耦合分析理論基礎,來設計符合料管輪廓的線圈樣式,以達到較佳的電磁熱耦合效率。由於射出機料管的幾何形狀為長條狀的圓柱,所以需要多區段的加熱器來加熱,故需優先考慮軸/ 徑向溫度均勻性與加熱效率。因此設計三款樣式感應線圈,後續將會針對電磁與溫度場形的比較,找出最佳的料管感應線圈樣式。第一款為螺旋型線圈,此樣式一線圈電流方向相同,環繞線圈匝數緊靠磁場有加成的效果,預期感應磁場較強,其幾何形狀如圖四樣式一所示。第二款為渦型線圈,可製作成扣合式較方便安裝,但最內圈電流方向不一樣可能會有磁場相抵銷的情況,其幾何形狀如圖五樣式二所示。第三款為階梯型線圈,兩側相鄰導線電流方向不一,推論在感影磁場與加熱效果皆較差,其幾何形狀如圖六樣式三所示。料管外經φ97mm,如圖四樣式一所示。而三款線圈內徑皆為φ100mm、線圈間距為7mm,故線圈與料管的感應距離為3mm,而其加熱區間為110mm。其線圈的材質為紅銅,料管的材質為結構鋼。
參數設定
針對螺旋型線圈、渦型線圈與階梯型線圈進行電磁熱耦合分析,研究三款感應線圈幾何形狀對圓柱體加熱場形之影響,並將加熱場形溫度較低之處放置導磁塊,目的為優化線圈之加熱場形。其線圈材料為紅銅,模具材料為結構鋼,導磁材料為鐵氧體,參數設定如下:
- 初始溫度=30℃
- 電流V=90[V]
- 頻率f=20~50[KHz]
- 線圈材質= 紅銅(99.9% 銅)
- 模具材質= 鋼
- 電阻率(鋼): 1.72e-8 Ωm
- 電阻率(銅): 2.48e-7 Ωm
- 溫度係數(1/K)(鋼):0.0039
- 溫度係數(1/K)(銅):0.005
- 導電率(銅)=5.998e7[S/m]
- 導電率( 鋼)=4.032e6[S/m]
- 導電率(導磁塊)= 1e-7[S/m]
- 相對導磁率(銅): 1
- 相對導磁率(鋼): 1000
- 相對導磁率(導磁塊): 3000
- 真空導磁率:4πe-7 N/A^2
- 常壓熱容(比熱容)(鋼): 475 J/(kg.K)
- 常壓熱容(比熱容)(銅): 385 J/(kg.K)
- 常壓熱容(比熱容)(導磁塊):700 J/(kg.K)
- 熱傳導係數(鋼): 44.5 W/(m.K)
- 熱傳導係數(銅): 400 W/(m.K)
- 熱傳導係數(導磁塊): 3.5 W/(m.K)
料管感應加熱模擬結果
料管感應加熱其應用原理是將頻率為60 Hz之市電引入系統,再利用加熱器之電源裝置,使其轉變成不同頻率的交流電源,並提供給負載部份之加熱線圈,使加熱線圈產生交變磁場。於此時再將一具有磁性或非磁性的導電加工物件置於加熱線圈所產生的交變磁場內,則由於磁力線的切割,導致在不同深淺的加工物件面上產生感應電流(即渦流),而使加工物件溫度升高,以達到加熱的目的(Davies E.J.,1995)。將以COMSOL多物理耦合分析軟體分析3D磁力線場形與3D加熱場形,再比較三款線圈的磁場與溫度相關數據,依據相關數據分別找出三款線圈加熱溫度不足之處,可使用導磁塊配置方式來優化三款線圈。
為了讓電磁熱耦合有最佳效率,因此加熱線圈與工件間的距離應愈近愈好,如此才能使較多的磁力線通過加工物件,因磁力線越密集,則加工物件所生成的感應電流越大。反之,則會造成線圈與加工物件間的磁漏大,加熱效果較差,因此三款線圈距料管的感應距離皆為3mm。從線圈(樣式一/二/三)磁場分析圖來觀察,如圖七與圖八所示,線圈樣式一與樣式二其電流方向較為一致,整個磁力線分布較容易結合在一起,而圖九樣式三則因線圈電流流向不同,磁力線分布較不容易結合且有分區塊的情況。為探究線圈磁力線對料管之影響,擷取料管徑向面的磁力線分布。樣式一的截面磁力線分布整齊且方向一致,樣式二與樣式三的截面磁力線分布就顯得較混亂,且磁力線方向較無規律。三款樣式線圈磁場強度(H)皆在6000A/m以上,最大磁通密度(B)皆在0.3T以上,但從這兩項數據還無法判定哪一款線圈的加熱效率最佳,因還有磁熱耦合因素,必須從料管的加熱場形來探討。
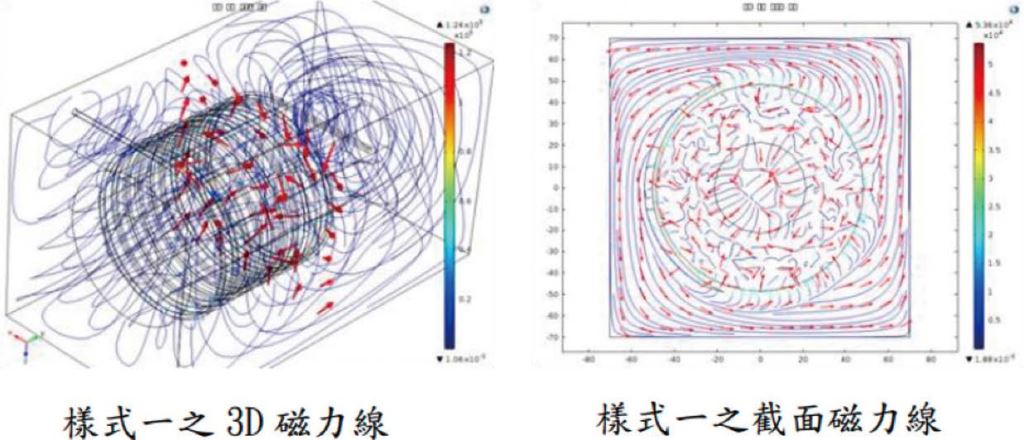
圖七、線圈(樣式一:螺旋形線圈)磁場分析圖
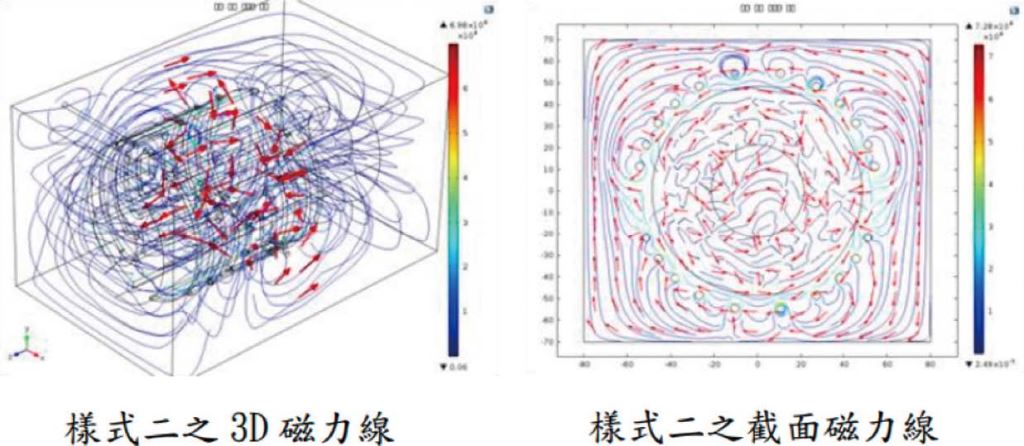
圖八、線圈(樣式二:渦形線圈)磁場分析圖
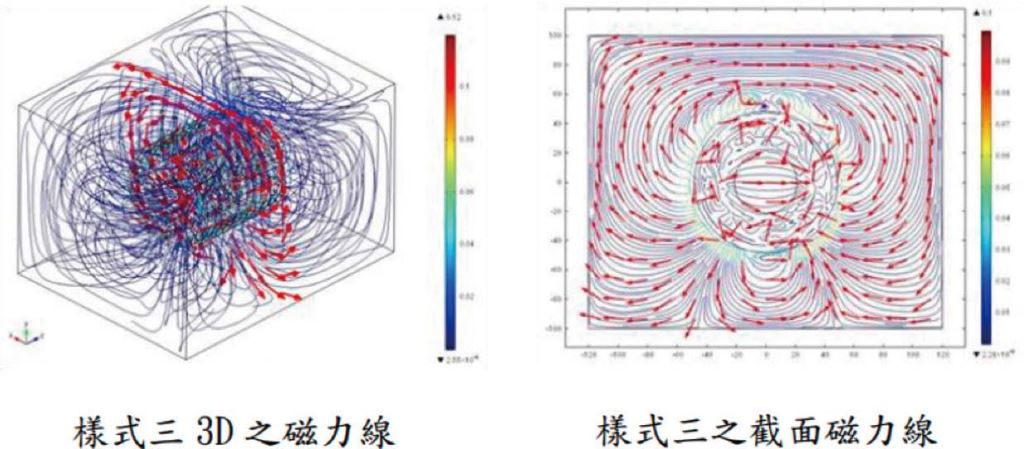
圖九、線圈(樣式三:階梯形線圈)磁場分析圖
因料管溫度上升是由於電磁損耗所造成的,換言之料管溫度的能量來自於渦流損耗。故軟體在分析時,需先透過電磁分析求出渦流損,再將渦流損的結果轉至熱傳分析模組作為熱源,並以求出料管的溫度,之後在將所求的溫度代回電磁分析中,取得在此溫度下的電阻值,再繼續求解,如此重複至目標時間。整個軟體分析流程稱為電磁熱耦合分析。其中磁熱耦合分析結果為線圈(樣式一/二/三)之料管加熱場形,如圖十所示。將三款樣式線圈的溫度場分布做比較,以線圈樣式一的溫度場分布之均勻性最佳,但前後末端的溫度略低於平均溫度值,線圈中端的加熱分布為全區最高。次佳的溫度場分布為 線圈樣式二,從料管側邊來看,在矩形線圈的四周角落為溫度較低之處,最內圈也因電流方向不同產生磁場抵消,故溫度也較低,另外在兩組線圈組合端亦是溫度較低的地方。最差的溫度場分布則屬線圈樣式三,因為其相鄰線圈電流大部分皆為不同向,僅有兩組線圈組合端部分線圈電流同向,故只有電流同向部分加熱溫度較高,其它處溫度皆低。接下來我們統計三款樣式線圈的軸/ 徑向溫度數據,線圈樣式一的軸向溫度分布:最大溫度為222.86℃、最小溫度為119.65℃、平均溫度為195.76℃與平均溫升為165.76℃。 而樣式一的徑向溫度分布:最大溫度為215.27℃、最小溫度為211.72℃、平均溫度為 214.22℃、與平均溫升184.22℃,其軸/ 徑向溫度分布數據皆為三款樣式線圈最佳。
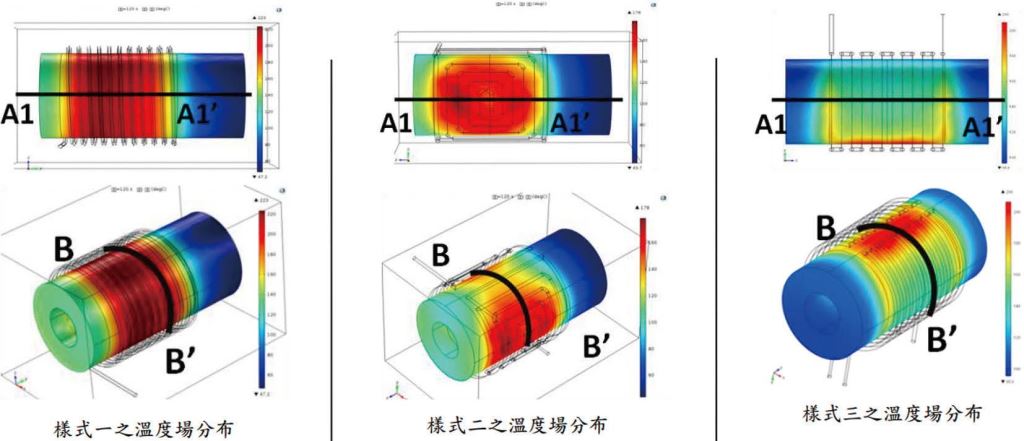
圖十、線圈(樣式一/二/三)之料管加熱場形分析圖
▋ 用於感應加熱電路之全橋逆變器
交直流轉換電路
交直流轉換電路,如圖十一所示,包括輸入無熔絲開關、突波吸收器、緩啟動電路、整流電路、穩壓電容、限流電阻與交直流轉換介面電路,並進行電路測試,輸入一電壓為AC407V,可量得輸出DC電壓為569V,如圖十二所示。因考量電源啟動瞬間穩壓電容之充電電流過大,故加上緩啟動電路,其做法為:於穩壓電容前端加上限流電阻,以降低啟動電流,且考量全功率輸出時,限流電阻會消耗能量,故於限流電阻兩旁加上旁路電路,降低功率消耗。
突波吸收器可防止大於1.3倍或1.5倍之電壓突波進入感應加熱模組內部;緩啟動電路之目的為避免啟動電阻於全功率輸出時消耗多餘的電力,故於穩壓電容充飽電後,透過旁路電路將限流電阻短路,以降低能耗;整流電路是將前端之三相交流電源,轉換為全波整流訊號,並透過穩壓電容將此訊號轉換為直流電源,當系統關電時,穩壓電容仍具殘餘電荷,故須使用放電電阻進行放電,以增加電路安全性;交直流轉換介面電路用途為當緩啟動電路於全功率輸出時,將限流電阻短路,並做為電路隔離之用途,避免主線路的雜訊影響到控制電路之電源。
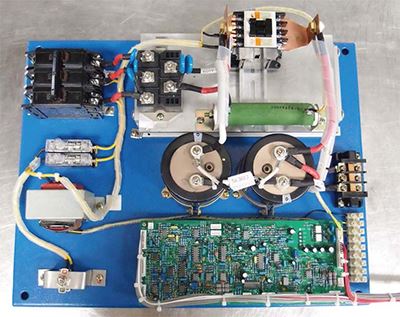
圖十一、交直流轉換電路模組 |
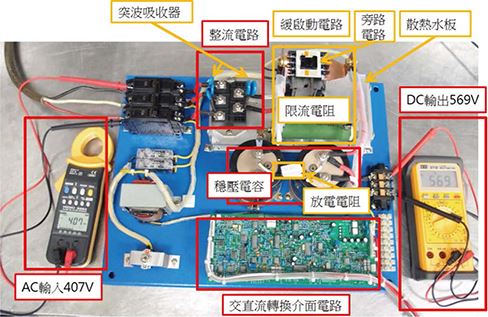
圖十二、交直流轉換電路模組量測結果 |
降壓轉換電路
降壓電路,如圖十三所示,設計規格為:輸入569Vdc±10%、輸出電壓60Vdc±10%,使用功率電晶體、降壓介面電路、電流讀取介面電路、二極體、降壓電感器等元件,將高壓直流電源569VDC 降至低壓直流電源60VDC,如圖十四所示,降低輸出之功率,達到以低功率輸出進行阻抗匹配之目的。另外,將功率計架設於電源輸入側,可量得降壓電路之功率為1.093kW。
功率電晶體為絕緣閘雙極電晶體(IGBT),功率電晶體的輸入端以脈波寬度調變(PWM)訊號加以控制,以脈波寬度控制來調整降壓電路輸出電壓之大小。當IGBT導通時,二極體為逆向偏壓,此時電流流經降壓電感器,使輸出電容被充電,而在IGBT為截止時間內,此時降壓電感器兩端電壓極性相反,以保持電流流經降壓電感,使得二極體順向而導通,所以原本在電容器中所儲存的能量,就可經由降壓電感器和二極體釋放至負載上,透過控制功率電晶體對電容的充放電的時間與能量,達到降壓的目的;電流讀取介面電路讀取CT 比流器之數據,透過放大器、比較器與邏輯閘電路,再將結果輸入至微控器進行輸入電流判讀;降壓介面電路之目的為控制功率電晶體IGBT 之輸入訊號脈波寬度大小,達到降低電壓之目的,驅動功率電晶體IGBT,將微控器所輸出的控制小訊號,放大到可驅動功率電晶體IGBT 之驅動電壓,並且做為隔離功率輸出電源與控制電源隔離之目的。
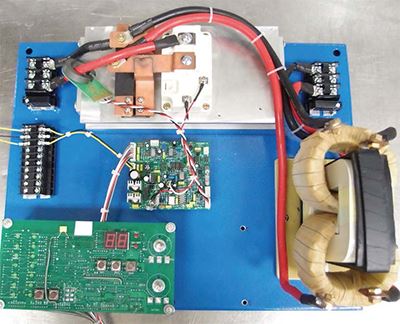
圖十三、降壓電路模組 |
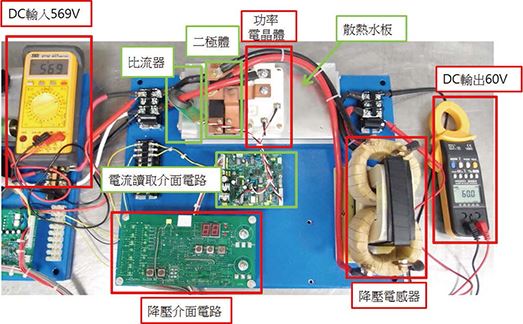
圖十四、降壓電路量測圖 |
3.3全橋逆變電路
全橋逆變電路,如圖十五所示,運用光耦合隔離驅動電路驅動功率電晶體IGBT,且使用適合用於全橋逆變電路的IGBT 半橋模組,其耐壓為1200V,耐流為300A,將兩個半橋模組組合成全橋IGBT模組,並搭配周邊電路,經由實測結果得知,加入電感性負載,全橋逆變電路可測得30.878kW之功率。
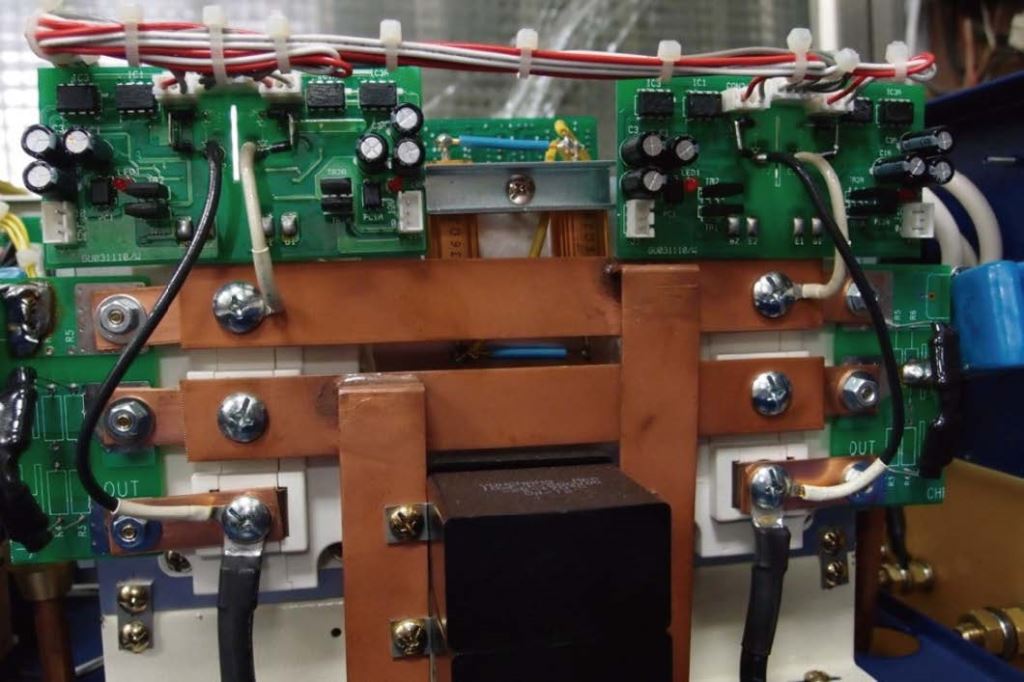
圖十五、全橋逆變電路
▋ 結論
加熱相關工業是支持製造業生產的重要產業,於加熱技術的選擇上,主要考量因素包含能耗、能源使用效率、加熱溫度、加熱速度、加熱均勻性等。近年來全球在加熱技術發展趨勢,已逐步收斂至感應式加熱裝置的應用,相較於傳統加熱製程技術,感應式加熱技術具有加熱速度快、節省能耗、品質及產能效率提升等優勢。於加熱相關工業導入感應式加熱電路設計技術所製作的加熱器,可提升感應加熱器業者設備、金屬熱加工業者與橡塑膠業者銷售之毛利率,更可以節省加工所產生的大量能耗、降低生產成本,如可大力推廣感應加熱逆變電路設計技術於各式工業加熱器,並使感應式加熱技術於各加熱相關工業普及化,必能為我國工業節能方面創造更多的節能減碳效益。本文針對料管感應線圈設計三款樣式,將其三款樣式線圈進行電磁熱耦合分析,探討其不同幾何形狀的線圈,在感應磁場與加熱場形之優劣特性,以找出最適合用於料管感應加熱的線圈幾何形狀。並對其特性以導磁材料優化,目的在於強化三款線圈的加熱場形之均溫性,透過模擬找出最適合的線圈構型,搭配全橋逆變電源主機技術,使加熱速度加快,使塑橡膠機台更節能,對於塑橡膠節能技術上,針對感應加熱技術進行業界推廣,隨著全球環保意識抬頭,上游品牌公司(例如:Apple、Samsung、ASUS)對於環境責任越來越重視,紛紛要求產業鏈下游供應商採用節能與環保的綠色製造技術,面對新的產業環境,綠色製造科技的發展與導入,做到塑 橡膠整廠工作站生產單元製造過程節能、節料、精簡製程、降低不良率、提高加工速度乃至人力都是當前國內塑橡膠成形產業發展迫切需解決之問題。
▋ 謝誌
本研究計畫承蒙經濟部能源局提供經費補助(計畫編號112-E0204),特此致謝。
▋ 參考文獻
- 陳民山,“射出機螺桿感應加熱的實驗與分析”,成功大學機械工程學系,碩士論文,2012。
- 李育芸,“感應加熱應用於模具快速加熱之研究”,中原大學機械工程學系,碩士論文,2002。
- 陳秋君,“含加熱系統模具模溫之模擬與驗證”,中原大學機械工程研究所,碩士論文,2001。
- 濱田修,“射出成型之模溫控制技術”,模具工業雜誌,1993。
- A. Hobson ,“Physics 5th Editor”, Pearson College Div, 2009.
- E. Horoszko, Krakớw, Polen, “Induction Heating of Flat Objects”, Arch. f. Elektvotechn., Bd.57, H 3, 1975.
- E.J. Davies, “Conduction and Induction Heating”, IET Power Engineering Series 1st Edition,1990.
- M. H. Tavakoli, H. Karbaschi and F. Samavat, “Influence of workpiece height on the induction heating process”, Mathematical and Computer Modelling 54 (2011) 50–58.
- M. Kranjc, A. Zupanic, D. Miklavcic and T. Jarm, “Numerical analysis and thermographic investigation of induction heating“, International Journal of Heatand Mass Transfer 53(2010)3585–3591
- Davies E.J. and Simpson P.G.., “Induction Heating Handbook”, Mcgraw-Hill Book company Ltd., London(1995)
- 陳建興,“全橋相移式高頻溫控感應加熱器之設計與研製”,中原大學電機工程學系,碩士論文,2005。
- 林正宏,“1 kW 全橋相移式升壓型零電壓切換轉換器之研製”,第三十一屆電力電子研討會,2010。
- 何秀華,“大功率 IGBT 驅動電路設計”,南京電子技術研究所,2008。
- FUJI Electric“閘極驅動電路設計方法”,技術資料。
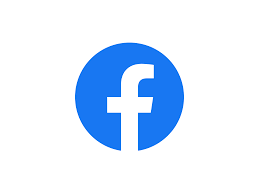 |
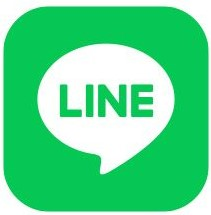 |