五軸加工機擁有高度靈活特性,可加工複雜工件,減少治具與工件轉換之停滯時間,可提升 加工效率、縮短製程時間與提升刀具壽命等優點,五軸加工機已是現今高精密、高品質工 件製作不可或缺的機種之一。
工具機幾何精度與性能對於加工品質擁有相當的影響性,精機中心本次針對工具機廠所新製 的五軸工具機之空間精度進行量測,共計進行27 台五軸工具機的精度檢測,其中包含動柱式13 台、天車式9 台與龍門式5 台,檢驗項目主要有線性軸6 自由度誤差、旋轉軸定位精度、循圓測 試、立體空間對角線分析、R-Test 刀尖跟隨同動精度,相關精度誤差分析與參考規範如表一所示, 本文將以動柱式機型為主體,針對測試方法、測試標準、量測結果等,進行說明與探討,如對業 界對於機器現象或是測試方法有興趣,歡迎與精機中心交流。
▋ 工具機構型與角度誤差定義說明
五軸工具機機型大致上可區分為三類:
- 兩旋轉主軸頭(Head-Head)
- 兩旋轉工作台(table-table)
- 一旋轉主軸一旋轉工作台(Head- table)
五軸機型中,動柱式機型與天車式機型皆為兩旋轉工作台(table-table) 機型,如圖一所 示,以刀具右手定則定義機械座標系,動柱式機型,搖擺軸為繞著Y 軸旋轉,定義為B 軸,旋 轉軸圍繞著Z 軸旋轉定義為C 軸,整體軸向定義為X、Y、Z、B、C;天車式機型,搖擺軸為 繞著X 軸旋轉,定義為A 軸,旋轉軸圍繞著Z 軸旋轉定義為C 軸。

圖一、 動柱式五軸機構型(左)與天車式五軸機構型(右)
五軸機精度檢驗,本文中其角度誤差均以〝角秒〞表示,如圖二所示,1 度60 角分(arcmin); 1 角分60 角秒(arc-sec);1 度為3600 角秒,即一角秒約0.000278 度,如以氣泡式 水平儀表示,如圖三所示,泡式水平儀一格為0.02mm/m ≒ 4 角秒,或是0.005mm/m(1/4 格)≒ 1 角秒。
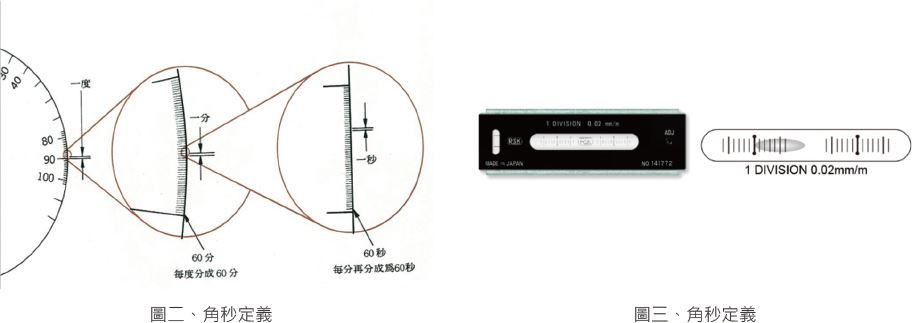
圖一、 動柱式五軸機構型(左)與天車式五軸機構型(右)
▋ 標準規範與測試數據解析探討
針對各項測試之量測手法,參考標準與量測結果進行分析探討,其量測結果以最大最小值, 與正規化數值進行解析探討。
線性軸6 項自由度誤差
五軸工具機一般含有三個線性軸以及兩個旋轉軸,根據ISO 230-1 國際標準定義,五軸機工 具機誤差項目分為21 個線性軸誤差及22 個旋轉軸誤差,並以元件誤差(component error) 及 位置誤差(location error) 來定義,三軸線性結構以線性軸分為18 個元件誤差,另加上三線軸組 裝後之3 個位置誤差,即垂直度,所以三軸線性結構共具有21 個誤差項,其中單一線性軸包含 Pitch、Yaw、Roll(角度誤差),平移誤差,包含水平向真直度、垂直向真直度及定位精度等6 個自由度誤差,如圖四所示,本次測試透過Renishaw XM-60 (6D Laser) 進行量測,如圖五所示, 單一線性軸量測,可同時量測並解析6 個自由度誤差,有別傳統量測方法,測試結果根據ISO 10791-2 (2023) 標準規範允收值進行誤差分析,如表二、表三所示,其中EXX、EYY、EZZ 為定 位精度,可參考ISO 10791-4 標準規範。
單軸自由度測試結果如圖六所示,定位精度誤差,EXX 最大誤差約:17μm,最小誤差約: 2μm;EYY 最大誤差約:15μm,最小誤差約:2μm;EZZ 最大誤差約:12μm,最小誤差: 2μm,皆符合ISO 19791-4 標準規範,雙向定位精度28μm 之允收值;平移方向最大誤差為 EZY 約為13μm,最小誤為EXY 約為1μm。
旋轉方向誤差,大多符合ISO 10791-2,其中X 軸向最大誤差為EBX 約13〞,最小誤差為 EAX 約1〞;其中Y 軸向最大誤差為EBY 約8〞,最小誤差為EBY 約1〞;其中Z 軸向最大誤差 為EAZ 約13〞,最小誤差為ECZ 約2〞。
由於動柱式五軸機構型,X 軸向須背負滑座、鞍座、頭座等Y、Z 軸結件重量,如圖一所示, 因此X 軸向時運行時,因受質量與慣性力等緣故,使得EBX 角度誤差大,如圖七所示,將X 軸 旋轉自由度誤差值正規化,大多機台EBX 誤差會大於EAX 與ECX,此外在量測單軸自由度時, 同時於不動件(工作台)架設電子水平儀,量測工作台動態水平,相關測試結果進行正規化後, 如圖八所示,由測試結果顯示,當移動X 軸向時,工作台雖然為固定不動,但還是會受到移動件 慣量的影響,能會導致EBX 誤差較大。
旋轉軸定位精度
旋轉軸定位精度使用Renishaw XL-80 與XR-20 進行量測,如圖九所示,定位精度量測方 式是依據ISO 230-2 標準規範進行量測與計算誤差,允收標準可參考ISO 10791-4 標準規範, 如圖十所示,旋轉軸雙向定位精度應在28" 內,單向定位精度應在22" 內。旋轉軸定位精度 誤差結果如圖十一所示,整體而言搖擺軸整體誤差大於C 軸,由測試結果顯示,C 軸無論有無 clamping,誤差皆在20" 內,符合ISO 10791-4 允收標準,B 軸無clamping 時,最大誤差約 為27",當clamping 時,最大誤差約為38", 透過測試結果顯示,當旋轉軸clamping 時,定 位精度與未clamping 差異較大時,建議可調整旋轉軸剎車,使定位精符合允收標準,提高加工 品質。

圖九、旋轉軸定位量測圖
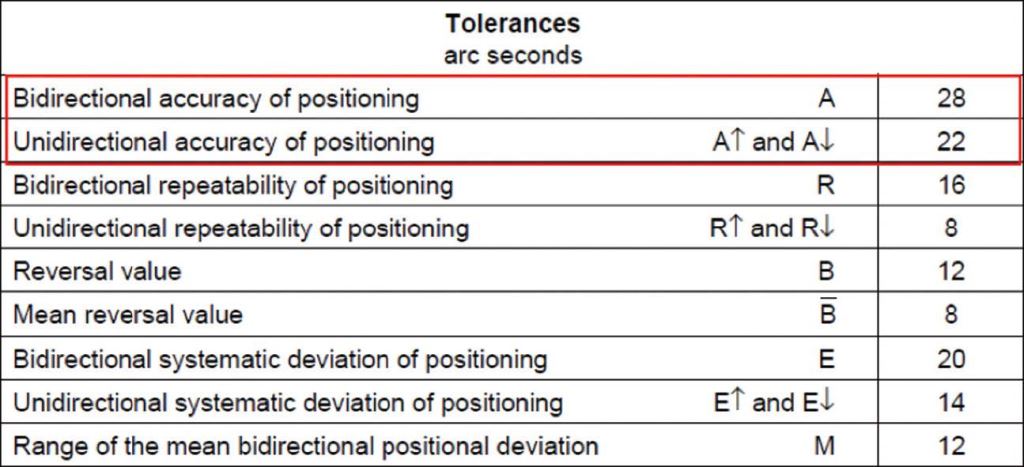
圖十、ISO 10791-4 旋轉軸定位精度誤差範圍
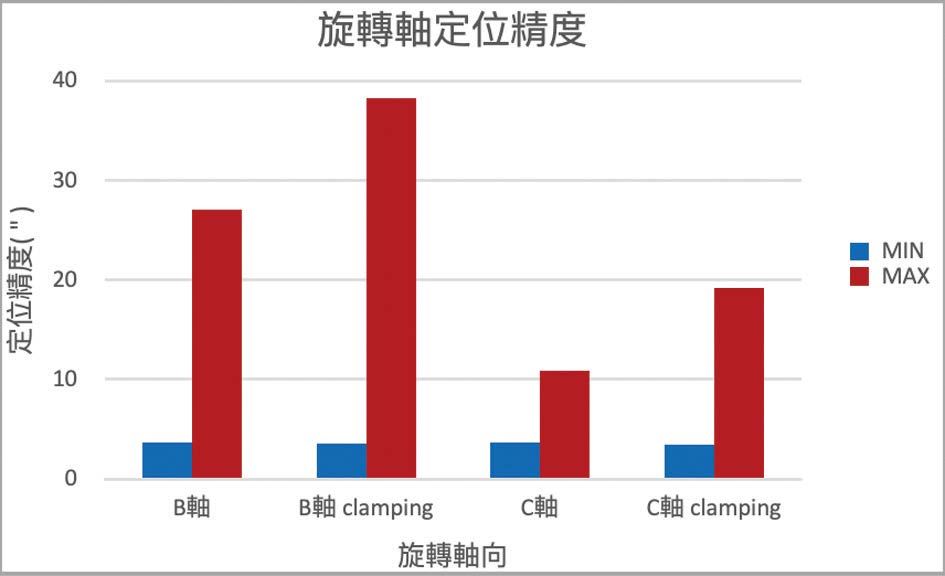
圖十一、 旋轉軸定位精度誤差數據圖
循圓測試 循圓測試使用Renishaw QC-20 進行量測,相關測試條件與允收標準可參考ISO 10791-6, 如表四所示,本次測試條件如下列所示:
- XY 平面:量測角度:360 度 進給速度(F):1000mm/min
- YZ 平面:量測角度:220 度 進給速度(F):1000mm/min
- YZ 平面:量測角度:220 度 進給速度(F):1000mm/min
真圓度誤差分析
真圓度誤差主要是依據ISO 230-4 標準規範定義,進行圓度誤差分析,如圖十二所示,真圓 度無差為單一實際循圓軌跡,利用最小平方法求得虛擬圓心後,以此圓心當為基準進行畫圓,其 循圓軌跡之最小內切圓與最大外接圓之半徑差,即為真圓度誤差。
真圓度誤差分析結果如圖十三所示,由測試結果顯示,三平面真圓度誤差皆在30μm 以內, 符合ISO 10791-6 允收標準,整體而言XY 平面優於YZ、XZ 本次測試結果XY 平面最大誤差約 為10μm,最小誤差約為4μm,XZ 平面最大誤差約為18μm,最小誤差約為6μm,YZ 平面最 大誤差約為14μm,最小誤差約為7μm。
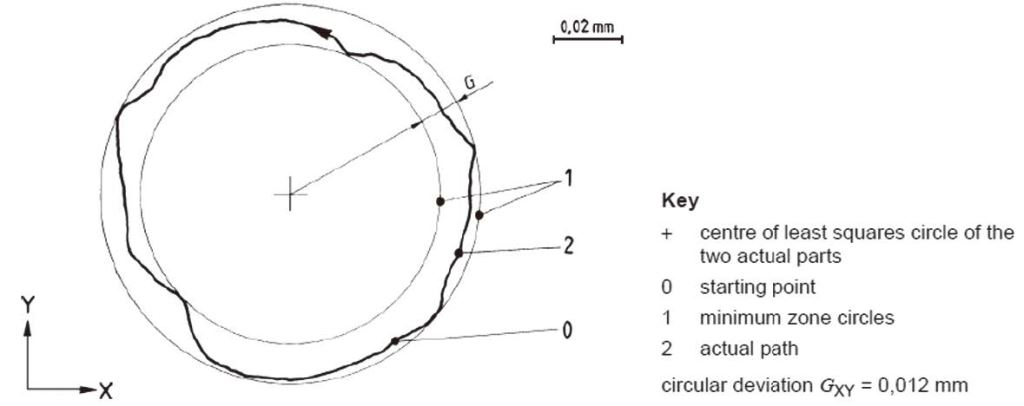
圖十二、 ISO 230-4 真圓度誤差定義圖
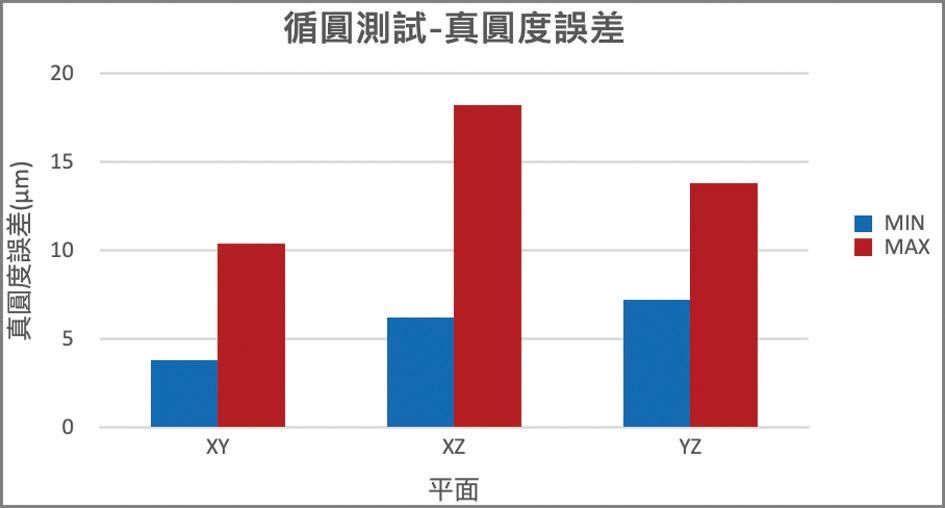
圖十三、循圓誤差數據圖
立體空間4 條對角線分析
立體空間4 條對角線精度量測,使用儀器為Renishaw XL-80,如圖十四所示,主要是依據ISO 230-6,如圖十五所示,為D1、D2、D3、D4 路徑,其量測點數每米至少 5 點,測速路度須小於最高進給速率之20%,相關量測方式可參考ISO 230-2 定位精度檢驗方式。
量測空間精度,建議以增量式量測,架設起點座標為P1 (X1,Y1,Z1),終點座標為P2 (X2,Y2,Z2), 量測長度(D) 可透過公式1 計算。
每個量測位置單軸向所需移動的距離,可以通過公式計算,以X 軸為例,利用公式(2) 計算 出X 軸的總距離(XV),求得X 軸向移動總距離後,可透過公式(3) 求得X 軸單次點位移動距離(IX), Y、Z 軸向以此類推。
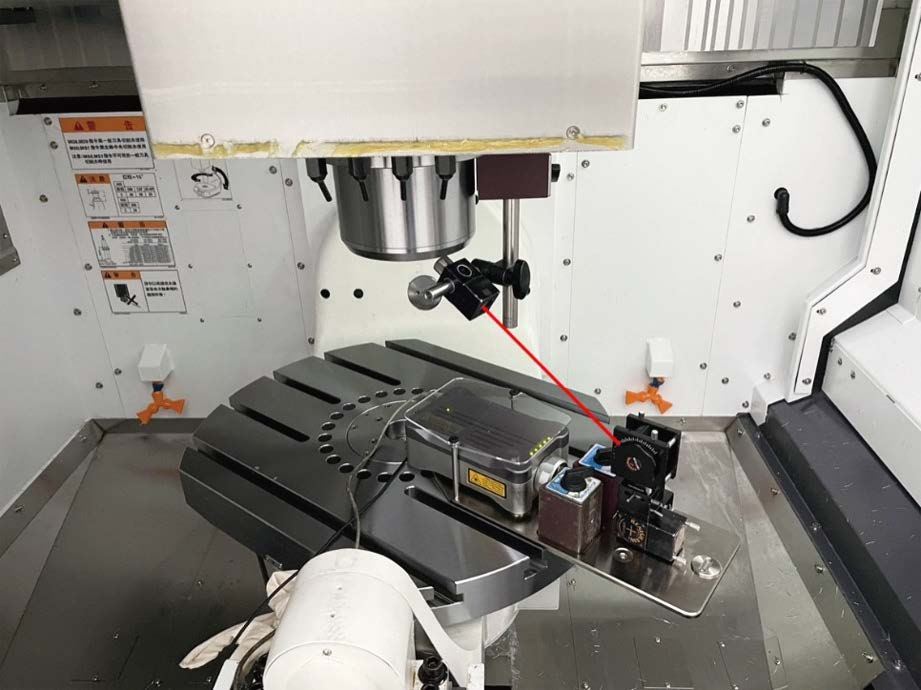
圖十四、對角線空間精度量測圖
對角線空間精度量測,標準規範並無規定允收數值,本次測試結果如圖十六所示,整體誤差 差約在30μm 以內,D1 最大誤差約為25μm,最小誤差約為6μm;D2 最大誤差約為30μm, 最小誤差約為7μm;D3 最大誤差約為27μm,最小誤差約為6μm;D4 最大誤差約為28μm, 最小誤差約為5μm。
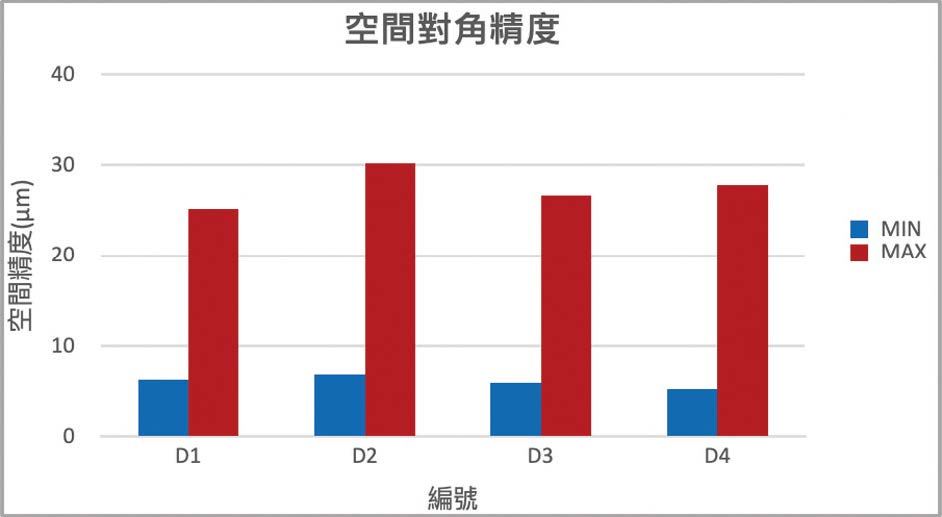
圖十六、 ISO 230-6 對角線空間精度量測結果
刀尖跟隨同動精度
刀尖跟隨同度誤差是使用IBS R-Test 進行量測,如圖十七所示,量測路徑參考ISO 10791-6 路徑,如圖十八所示,區分為BK1、BK2、BK4 三種路徑,以動柱式搖籃式五軸機型為例。
BK1 為搖擺軸(B 軸) 與XZ 軸同動之刀尖跟隨路徑(XZB),ISO 10791-6 建議速度為360˚/ min,量測角度建議大於90˚,或者因干涉所可運行之最大行程,並且需量測順時針與逆時針方 向,或由製造商與購買者協議。
BK2 為旋轉軸(C 軸) 與XY 軸同動之刀尖跟隨路徑(XYC) 建議速度為360˚/min,量測角度 建議360 ˚ 並且需量測順時針與逆時針方向,或由製造商與購買者協議。
BK4 為搖擺軸(B 軸)、旋轉軸(C 軸) 與XYZ 軸同動之刀尖跟隨路徑(XYZBC),議速度為 360˚/min,或由製造商與購買者協議。
刀尖跟隨誤差目前ISO 並無標準允收值,僅提供測試方法,相關測試結果如圖十九所示,本 次測試BK1 最大誤差約為:67μm,最小誤差約為:12μm;BK2 最大誤差約為:54μm,最小 誤差約為:11μm;BK4 最大誤差約為:54μm,最小誤差約為:16μm,BK4 精度誤差會受到 BK1 與BK2 精度誤差影響,一般而言當BK1 與BK2 精度誤差越小,其BK4 精度誤差也會較小。
刀尖跟隨誤差為綜合性誤差結果,可將精度誤差原因歸類為幾何精度、旋轉中心與電控參數 三大類,如圖二十所示,當同動精度誤差不符合廠內標準時,可先進行旋轉中心補償與參數調整 進行優化,再透過如自由度測試、空間精度測試、定位精度測試等,解析誤差原因進行相關調整, 優化刀尖同動精度,提升加工品質。
於廠商個別案例中如圖二十一、a. 所示,為BK1 靜態同動精度量測,同動軸向為XZB 軸, 由測試結果顯示,最大總和誤差為:126.3μm,分析為旋轉中心誤差過大所導致,經進行旋轉 中心位置補償後,再進行量測,測試結果如圖二十一、b. 所示,最大總和誤差為:11.05μm, BK1 動態誤差如圖二十一、c. 所示,最大總和誤差為:12.5μm(無計算反向尖點,但同動加 工時仍會有一痕跡),此外從圖二十一、b. 測試結果顯示,當執行BK1 測試時,路徑為B 軸 在XZ 平面上進行,不應有Y 方向之誤差量,但Y 軸仍有約7.6μm 誤差,並會隨著B 軸旋轉角 度呈線性分布,研判主要原因可能為B 軸軸線與Y 軸不平行所造成;執行BK2 靜態測試時, 同動軸向為XYC 軸,由測試結果顯示,最大總和誤差為:32.4μm,誤差值過大,測試結果如 圖二十一、d. 所示,經旋轉中心補償後,測試結果如圖二十一、e. 所示,最大總和誤差為: 10.4μm,精度誤差有明顯改善,但由測試結果顯示Z 軸向能會因C 軸位置變化呈現線性分布, 主要原因可能為Y 軸自重下垂,導致C 軸與Z 軸平行度的誤差,BK2 動態誤差如圖二十一、f. 所 示,最大總和誤差為:13.2μm(無計算反向尖點,但同動加工時仍會有一痕跡),BK4 五軸同 動動態誤差如圖二十一、g. 所示,最大總和誤差為:18.2μm(無計算反向尖點,但同動加工時 仍會有一痕跡)
▋ 結論
- 本次的精度調查結果,可發現國內工具機業者所生產製造的五軸工具機,其精度誤差大多符 合ISO 10791 相關標準規範允收值,部分廠商已達到1/2 規範允收值。
- 旋轉軸定位精度量測,進行有clamping 跟無clamping 的量測,如兩者精度誤差太大,建議 可檢查煞車系統,無clamping 的精度主要會影響5 軸同動加工精度,有clamping 時,雖然 主要執行3+2 軸的粗加工或中胚加工,如定位精度差異太大,會造成切削過程每刃進給切削 量不穩定,使得刀具壽命的降低,此外如進行鑽孔加工時,亦有可能造成孔位位置度偏差或 圓柱度的偏差。
- 刀尖跟隨同動誤差檢測,建議先分別進行BK1、BK2 路徑量測,確認相關幾何精度與旋轉中 心是否補償正確,再進行BK4 路徑量測,以確保能檢測到機器正確應該之同動精度。
- 希望透過本次調查結果,協助業者日後再開發相關五軸機型時,可參考相關檢驗數據誤差範 圍,設定精度目標值,優化機台精度,往高品級工具機邁進,提升整體加工精度與品質。
- 精機中心對於工具機精度檢驗、設計及開發擁有相當豐富的經驗,無論是設計開發、問題探 討以及檢測相關均有豐富技術資源與技術團隊,皆有相關檢驗設備與標準規範,各位業界先 進,想針對檢驗技術探討、標準規範定義、精度誤差數據解析,或是相關精度檢驗需求,隨 時歡迎與精機中心聯繫。
▋ 參考文獻
- ISO 230-1 標準規範(2012 版)
- ISO 230-2 標準規範(2014 版)
- ISO 230-4 準規範(2005 版)
- ISO 230-6 標準規範(2002 版)
- ISO 1079-2 標準規範(2023 版)
- ISO 1079-4 標準規範(1998 版)
- ISO 1079-6 標準規範(2014 版)
- 黃智達,技術通報 286 期_ 離軸旋轉定位精度量測探討,精機中心
- 廖志偉,技術通報 294 期_ 提高產線價值導入年度校正與品質管制,精機中心
- 黃智達,技術通報 299 期_ 工具機定位精度與重複精度淺談,精機中心