塑橡膠成形產業之工作站生產單元製程,於加熱的時間,耗損了許多能量,而常用於加熱系
統之感應加熱技術,因應不同加熱物件於不同的溫度下,有不同的負載,故需要高頻感應
加熱系統來補償負載的偏移,感應加熱頻率掃描技術,主要針對塑橡膠成形製程之負載匹配與提
升功率之需求,以及中上游塑橡膠設備、模具製造業者、感應加熱主機製造業者之關鍵零組件技
術亟需提升,投入變頻監測控制關鍵零組件研發,並開發可依照負載端特性,自動調控感應加熱
電源主機功率輸出、優化主機加熱效率之功能,預計產出高頻電力量測監控模組與追頻式電源
模組,提升主機電能轉換效率至90%。於本文中提出一個15kHz~40kHz頻率追蹤方案與高頻
300kHz驅動方案,本文旨在發展應用於感應加熱系統之電力驅動模組,所提模組是以碳化矽型
功率電晶體為開關元件,並使用諧振電路、負載線圈電壓、電流偵測與控制迴路等設計可達到驅
動模組高電力轉換效率之功能。本文亦已發展溫度閉環之數位訊號處理迴路,該純數位溫控設計
流程有助於縮短產品研發時程,而單晶片的程式加密功能,亦可降低產品量產後被抄襲、複製之
可能性。
▋ 研究背景與動機
目前國際上有兩項塑橡膠成形產業節能的主要評斷標準,主要以歐盟「EUROMAP60.1」及
中國大陸「塑料注塑成形機能耗檢測和等級評定」,為現今業界規範塑橡膠產業節能的重要指標,
尤其針對射出成形製程與設備能耗的測試規範,並訂定能耗等級關鍵標章,以鼓勵成形產業廠商
精進節能製程及設備技術。相對於國外的節能規範,我國目前並無完整的推動政策或補助計畫,
做為臺灣做為全球第六大塑橡膠機械生產國及出口國,是十分急迫需要面對的議題,財團法人精密機械研究發展中心(PMC)投入感應式料管與模具加熱技術之開發,透過新技術之導入,推出
低能耗成形塑橡膠烘料技術再創新。
在高表面光澤度或微結構塑膠製品部分,則以光學、3C、家電、車輛等產業應用案例最為
顯著,因其外觀件(外殼)須表現終端產品設計質感,常使用高表面光澤度設計方式(例如:烤
漆面)展現,近來更常有利用微結構設計(例如:髮絲紋、特殊霧化等)應用例。這類製品的製
程技術,關鍵在於如何將模具表面微結構設計精確地成形在產品表面(亦即表面轉寫性),國外
業者多導入高溫成形製程技術(提高模具表面溫度,減緩塑料表面固化層)。而3C 產品趨勢部分,
已明確朝向輕、薄、短、小發展,外觀件在物理剛性不變的前提下,訴求更輕、更薄成為設計主流,
故纖維複合材料的應用亦為目前塑橡膠製品領先國重要發展方向與趨勢。
為了解決上述問題,傳統成形量產過程必須長時間運作電熱式料管加熱器、模溫機,花費許
多能源與時間,才能足夠提高模具溫度,增加熔膠在模具內的流動性。然而隨著全球環保意識抬
頭,上游品牌公司(例如:Apple、Samsung、ASUS)對於環境責任越來越重視,紛紛要求產
業鏈下游供應商採用節能與環保的綠色製造技術,面對新的產業環境,綠色製造科技的發展,適
時導入感應式模具加熱與感應式料管加熱技術(如圖一所示),做到塑橡膠整廠工作站生產單元
製造過程節能、節料、精簡製程、降低不良率、提高加工速度乃至人力都是當前國內塑橡膠成形
產業發展迫切需解決之問題。
以目前之工程技術來看,幾乎所有加熱過程都會使用電力與化石燃料,使用電力作為輸入能
源具有快速、乾淨、無噪音、無汙染等優點。與傳統電阻式加熱相比,感應加熱是目前最先進的
加熱方式之一,由於它的非接觸加熱特性,熱傳效率極高,因而被廣泛運用在家庭、工業中。
在家庭方面,感應加熱最常應用於家用電磁爐,藉由功能性與機動性主要分為可攜式與崁
入式電磁爐。可攜式電磁爐電路簡單,通常為單一負載並使用D 類放大器作為主電路架構,並
使用預定義的按鈕進行功率控制。然為求其經濟效益,往往無法對各式材質的鍋子進行相同功
率的加熱,舉例來說:在固定70kHz工作頻率下,使用相同直徑的多層鍋、琺瑯鍋與感應鍋
進行加熱,由於材質不同,家用電磁爐對其施加的功率分別為1050W、700W 與600W,這
對使用者來說,每換一種鍋具便需要按照經驗調整對應的火力大小,使用上相當不便,崁入式
電磁爐通常具有2-5個加熱線圈,並有較大的頻率操作範圍,整體上有較高的加熱功率,其電
路結構較複雜,具多種保護電路機制,能夠針對鍋種精密的調整火力大小,使用體驗上較無如
此大的落差,目前市面上大多由輸入功率進行閉迴路控制,雖精確度較差,但架構相當簡單、
成本低廉。然而如前所述,倘若以商業應用為例便可觀察到如此多的問題,在工業方面更是如
此,因此為彌補上述功率偏差,勢必需要設計量測系統進行閉迴路控制。今隨著碳化矽及氮化
鎵等寬能隙元件逐漸成熟,更低的導通阻抗與高切換速度與價格優勢,使電源轉換器能夠有更
多電路架構能被實現,並能夠維持原有架構前提下提升轉換效率,感應加熱不再是低成本效益
的加熱方式。
▋ 電路方塊
高頻感應加熱系統模組整合感應加熱主機,如圖一所示,由以下的電路方塊所組成:
- (1) 變頻演算控制電路:由數位訊號處理IC、PWM 測試電路與電源模組所組成,主要功能為進
行頻率閉迴路控制。
- (2) 諧振頻率動態偵測電路:由相位偵測電路、電壓電流擷取電路與電源模組所組成,主要功能
為進行諧振頻率偵測。
- (3) 數位類比轉換電路:由數位類比轉換IC、參考電壓IC 與電源模組所組成,主要功能為透過數
位改變類比電壓以進行頻率改變。
- (4) 全橋逆變電路:主要由接收微控器所輸出的控制訊號,將DC 直流電轉換成高頻之感應式交
流訊號,並透過輸出匹配器來加熱線圈負載。
- (5) 輸出匹配器:主要功能為匹配輸出負載,並配合適當的電容值與功率變壓器,達到輸出阻抗
匹配之功能。
- (6) 線圈負載:此線圈負載可以為模具內建線圈、外掛式線圈或料管線圈等加熱負載。
- (7) 溫度回授電路:主要進行線圈阻抗所加熱物之溫度閉回路控制,藉此電路達到每5℃進行頻率
追蹤一次。
- (8) 電流偵測電路:主要將全橋逆變電路或輸出匹配器的輸出電流透過電流偵測電路,輸入到電
壓電流落後超前檢知電路,進行電流與電壓落後或超前的程度之判讀。
- (9) 電壓偵測電路:主要將全橋逆變電路或輸出匹配器的輸出電壓透過電壓偵測電路,輸入到電
壓電流落後超前檢知電路,進行電壓與電流落後或超前的程度之判讀。
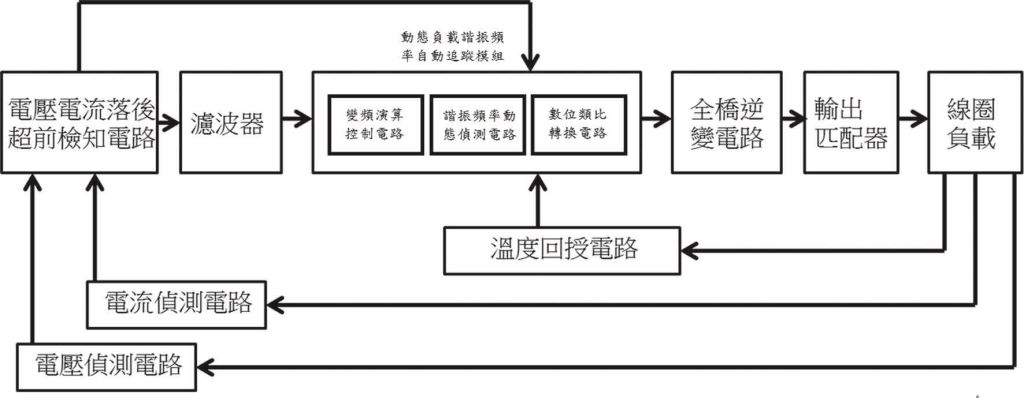
圖一、掃描控制模組電路方塊
▋ 感應加熱原理分析
感應加熱是基於電磁感應對導磁導電材料進行非接觸加熱,由法拉第定律可知,在時變磁場
中放置一根導線,導線兩端將產生與磁場變化相反的感應電動勢,此時若將導線短路,就能產生
感應電流。若將導線更換為一塊較大的導體時,如圖二所示,一個簡單的感應加熱裝置便完成了,
由於導體與磁場平行的面積增加,感應電流更容易在導體上自成迴路,此時的電流稱為渦電流,
如圖二所示,渦電流會與導體自身的阻抗產生功率,其中渦電流的大小決定加熱的速度,並與磁
場大小、導體電阻率、導體形狀相關。感應負載與線圈等效電路圖,如圖三所示,其可視為二次
側僅一匝之變壓器,其中Re為加熱線圈電阻、n為加熱線圈匝數。經簡化後,感應加熱負載可
視為一電感器,而電感值與線圈的幾何形狀相關。流過線圈的電流區分為兩個部分,一部分為磁
滯電流以及渦電流,另一部分則為激磁電流,其中渦電流佔大部分,其次為磁滯電流,對被加熱
物提供熱能,後者則無論有無負載時均會消耗電流,由於集膚效應的影響,當頻率越高時,越靠
近導線表面的部分電流越大,被加熱物也不例外,頻率每提升100倍,集膚深度就會減少10倍,
集膚深度示意圖,如圖四所示。
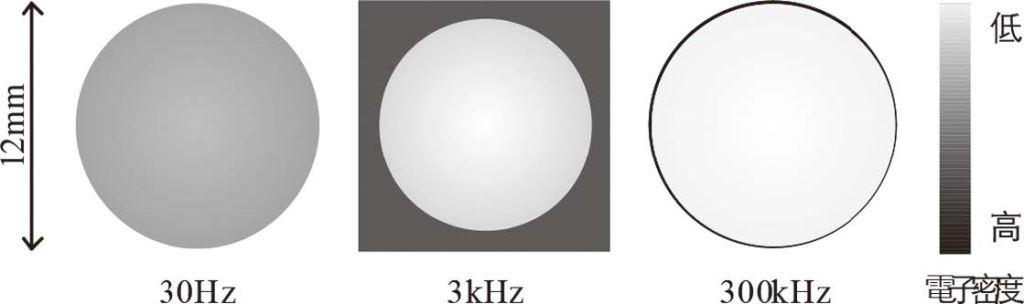
圖四、集膚深度示意圖(導線剖面)感應加熱負載等效模型
▋ 常見感應加熱電路架構
常見感應加熱電力驅動模組架構,如圖五所示,其中一般採用D類放大器作為電壓轉換
器架構。如圖所示經第一級轉換後的直流電壓將不會經過濾波器,而是直接由第二級電力轉換
器接入一個或多個感應負載,如此一來便不需要功率因數校正電路與體積龐大的濾波電容,進
而降低生產成本,且節省了壽命較短的直流濾波電容,此一設計往往更加耐用;但由於輸出波
形含高頻方波與低頻載波,因此輸出功率難以精準控制。再者,目前感應加熱的工作頻率約為20kHz~100kHz間,並由於使用極小的濾波電容,因此輸出將伴隨著100Hz或120Hz的電源
頻率,為量測該複合頻率的波形並計算功率,取樣頻率將會是很重要的因素,當取樣速度低於最
高工作頻率時,將無法獲得較佳的響應速度。
工業用感應加熱如電爐應用範圍包括電縫管熔接、高熔點合金爐、薄板加熱、鋼瓶淬火等,
將需耗費極大的能源,通常介於10kW到1MW間不等,此時可用的功率晶體及周邊元件將受到
物理極限的限制,適用的元件寥寥無幾,因此為了最佳化功率體積比,通常採用圖六架構,此架
構與圖五最大差異在第一級為具功率因數校正功能之直流升壓轉換器,以提供穩定直流源,第二
級為一直流降壓電路,藉由調整直流準位以控制輸出功率,最後再由多個功率晶體並聯的換流器
接到感應負載,在數百安培的情況下因集膚效應以及所使用導體的電阻率,將貢獻巨大的熱耗損,
也因此在這些應用場合大多使用水循環冷卻系統,藉此提升電力驅動模組的功率密度。
▋ 本文所設計之感應加熱系統
本文所研究之系統先將市電經全波整流與LC 濾波為直流電後,經電力驅動器操作轉換為高
頻方波,由負載匹配變壓器與諧振槽濾除高次諧波,使加熱線圈得到適當功率。本文驅動架構,
如圖七所示,由市電220V作為電源,經整流濾波得到一穩定直流,接著經過全橋換流器以及變
壓器輸出至負載端,並與諧振電容形成共振。諧振電路主要將換流器的方波,利用電感與電容諧
振來產生弦波形式電壓或電流,提供負載交變磁場,進而產生熱能。由於本文負載等效為一電感
串聯一電阻,故本文選擇使用串聯諧振電路作為諧振槽。值得注意的是,諧振槽品質因數Q越
大時,代表電感與電容跨壓越高,因此電容耐壓相當重要。
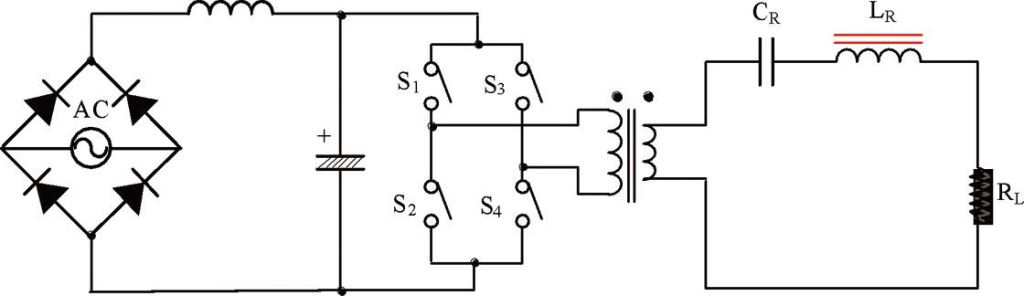
圖七、電路架構
溫度感測方面,以熱敏電阻、熱電偶較為常見,其中熱電偶的溫度係數較線性,且溫度量測
範圍較大,並有多種金屬材質供選擇。圖八為各種材質之熱電偶在不同溫度下的溫度係數,由圖
中可見在0℃ ~200℃間僅J-Type、K-Type較為線性(水平),又K-Type有較高溫度量測範圍,
因此廣受工業使用。本文將採用鐵氟龍披覆之K-TYPE 熱電偶,外層最高承受溫度200℃,具耐
熱、耐磨、防水優點,搭配TC77室溫偵測進行冷節點補償,可偵測最大200℃,若選用其他披
覆材質可承受更寬廣的溫度範圍。
圖九為K-Type熱電偶與PCB板接面示意圖,J1為量測端熱電偶產生之電壓,其溫度為
TC,J3與J4為兩處冷接點各別產生之電壓,其溫度為TREF,量測端因寄生接合(Parasitic
junction) 作用,可見J3與J4中不同材質分別與PCB板上的銅產生兩組不同梯度的熱電效應,
該電路VT所測得訊號為:
其中α為鎳矽合金與銅之熱電係數;β為鎳矽合金與鎳鉻合金之熱電係數;γ為鎳鉻合金與
銅之熱電係數。由(2)可看出該表示式必須知道3種不同金屬的熱電係數與參考點溫度,才能推
算出熱點溫度,在實作上雖能夠達成,但礙於各種材質熱電梯度對溫度皆不相同,如圖八所示,
實作上的誤差會較大。
綜合上述,本文設計之溫度控制方塊展開如圖十,單晶片從熱電偶接收到的電訊號經由AD
轉換器輸入第一階數位濾波器後,與冷端溫度相加算得物件實際溫度,再經由第二階數位濾波器
輸出至LCD監看窗,抑制加熱時產生的電磁干擾。另一方面將物件溫度與命令溫度輸入PI控制
器中,藉由計算得到修正值來控制PWM模組產生之DUTY訊號,控制功率大小,藉此控制物件
溫度,最後經物件上的熱電偶形成閉迴路控制。
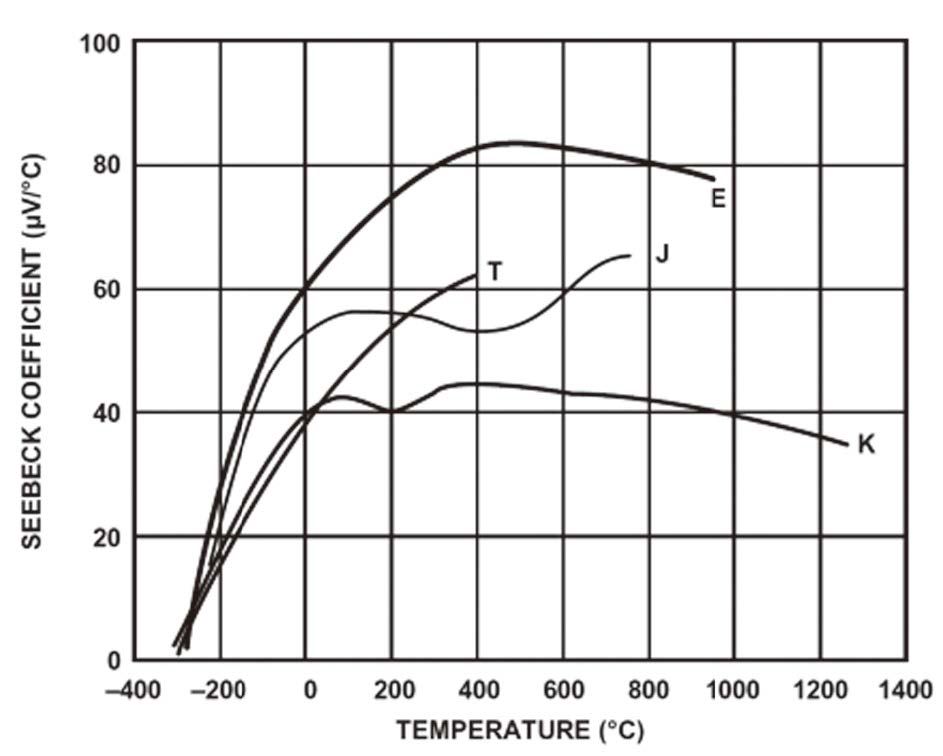
圖八、各種材質熱電偶對溫度關係[12]
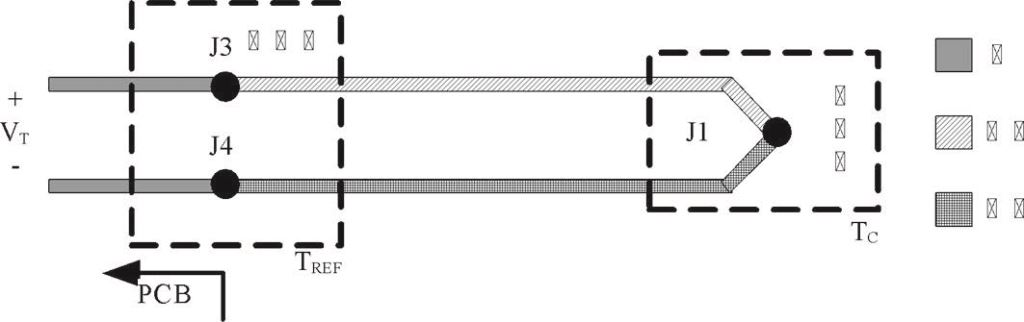
圖九、K 型熱電偶與PCB 連接
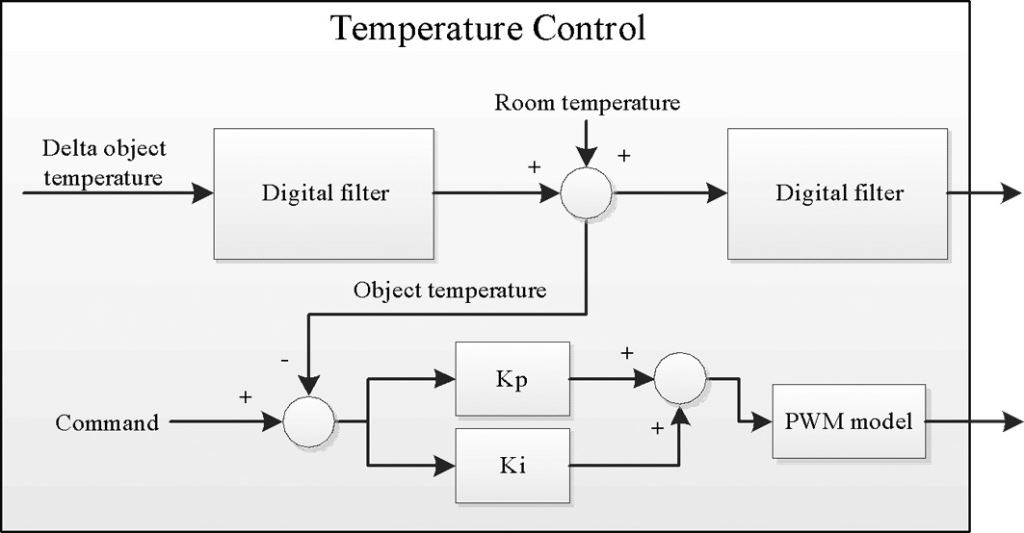
圖十、溫度控制程式方塊圖
▋ 負載諧振頻率自動追蹤設計流程與測試
於流程中介紹負載諧振頻率自動追蹤設計方法與技術、電路布局LAYOUT設計與搭配逆變
模組進行頻率與功率之測試,我們使用電路模擬軟體SIMPLIS來設計感應加熱電路。我們進行
15.4kHz~40.1kHz之頻率控制,並可由示波器看到輸出電壓電流波形相位差的訊號,於調整頻
率的同時,可藉由輸出電壓電流的波形與相位差,了解諧振頻率與負載特性,此技術使我們於加
熱線圈模具時,能找到適合的諧振頻率,成功達到提高加熱效率達90%。
(1) 追頻電路模擬
諧振頻率自動追蹤控制電路設計,如圖十一所示,其原理為:電壓與電流讀取電路所取得的
輸出電壓電流訊號,經過邏輯閘得到電壓與電流波形之相位差,再經由濾波電路將相位差脈波訊
號整流成直流電壓,由追頻控制電路將相位差脈波訊號改變IGBT功率電晶體之輸入控制頻率,
達到頻率自動追蹤控制的目的。
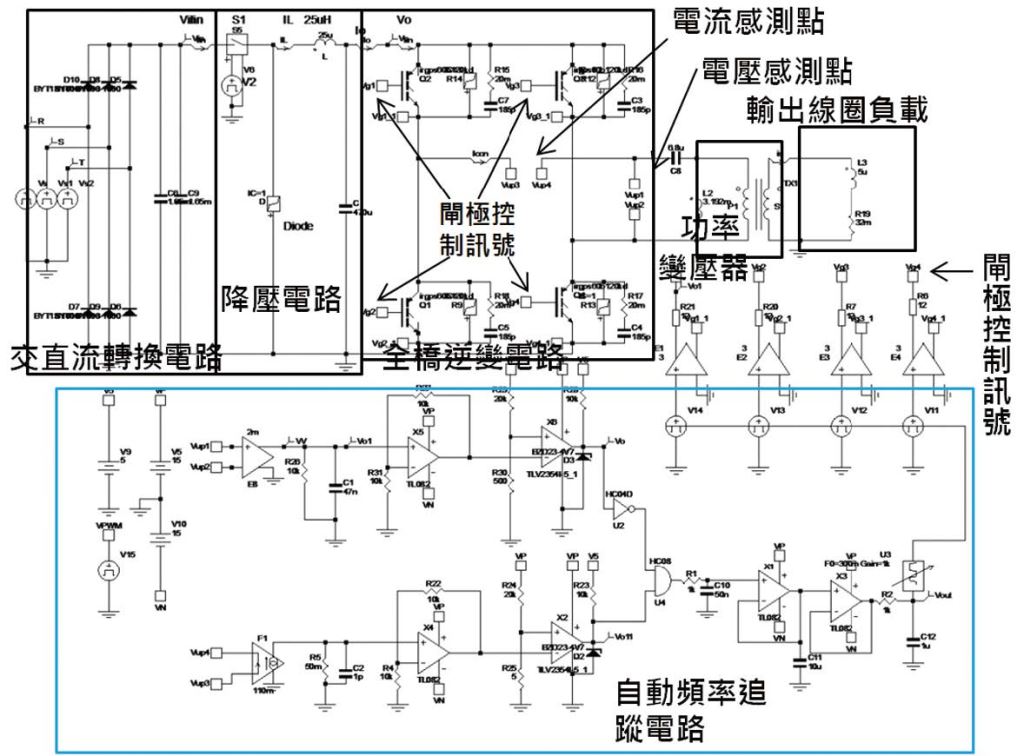
圖十一、諧振頻率自動追蹤調變模擬電路設計
利用SIMPLIS設計軟體,進行電路設計產出模擬電路圖,並進行電路模擬驗證電能轉換
效率,當輸入電壓為492.5V,輸入電流為54.4A,得到輸入功率為26.79kW;輸出電壓為
245.5V,由全橋逆變電路提供輸出電流為106.7A,相位角為22.7度,如圖十二所示,得到輸出
功率為24.16kW,將輸出功率除以輸入功率,得到電能轉換效率,由驗證結果可得知,電能轉換
效率可達90.2% (Pout=26.19 kVA* cos22.7 = 24.16 kW,Pin=26.79 kW,η=(24.16kW/26.79
kW)*100=90.2%),而透過追頻之模擬,可將功率修正30%回來,如圖十三所示,以彌補負載
加熱產生的電感偏移,並解決效率下降的問題,如圖十四所示。
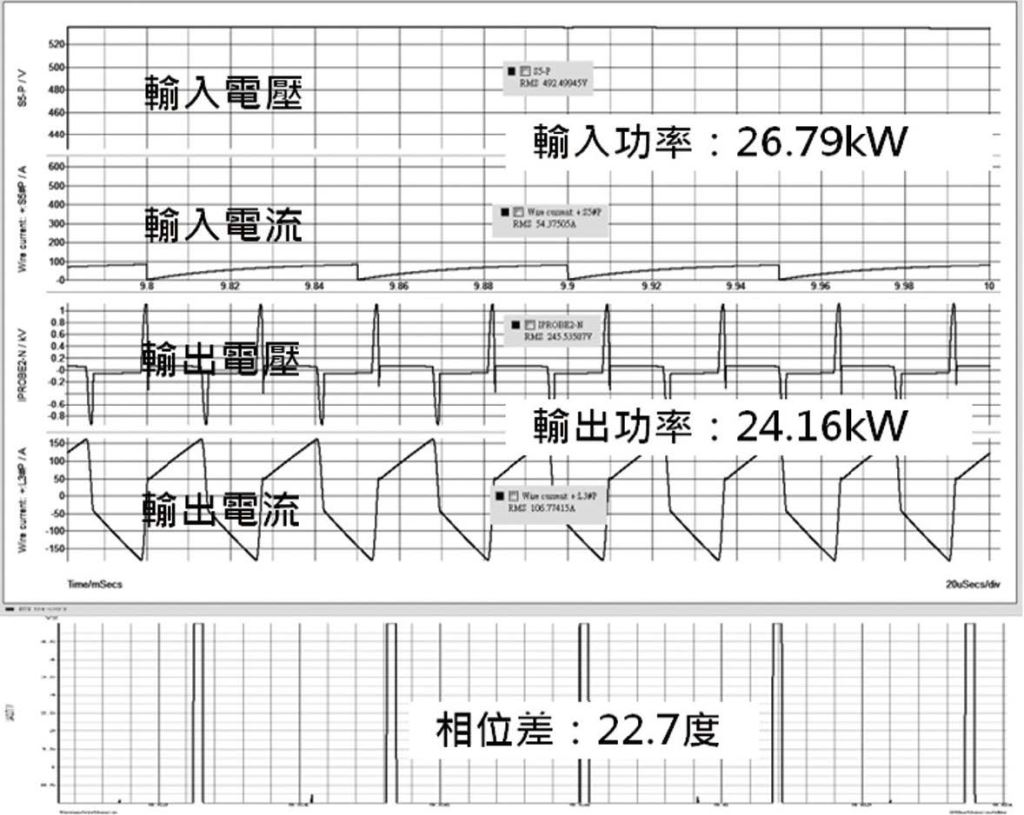
圖十二、諧振頻率自動追頻調變模擬電路波型
(2) 追頻式電源模組設計與穩態誤差測試
諧振頻率自動追蹤調變控制電路設計,使用Protel軟體進行控制電路LAYOUT 佈局設計,
產出追頻式電源模組,如圖十五所示,主架構包含:(1) 諧振頻率動態偵測電路:由相位偵測電
路、電壓電流擷取電路與電源模組所組成,主要功能為進行諧振頻率偵測。(2) 變頻演算控制電
路:由數位訊號處理IC、PWM測試電路與電源模組所組成,主要功能為進行頻率閉迴路控制。
(3) 數位類比轉換電路:由數位類比轉換IC、參考電壓IC與電源模組所組成,主要功能為透過數
位改變類比電壓以進行頻率改變。並產出追頻式電源模組電路圖、Layout佈局圖與PCB控制電
路板,使用電源供應器提供電路板電源,以訊號產生器,產生5kHz~ 40kHz之頻率,並透過追
頻程式之閉迴路控制,再經由示波器進行驗證,以追頻式電源模組透過搭配訊號產生器測試,實
驗數據統計追頻穩態誤差皆小於±0.92%,如圖十六所示。
(3) 頻率調整精度測試
完成諧振頻率自動掃描追蹤模組設計與製作,使用PWM 控制IC提供外部訊號,搭配數位
訊號處理晶片進行程式撰寫,透過數位類比轉換器產生5kHz~40kHz之頻率,並透過追頻程式
之閉迴路控制,改變頻率以量測頻率調整精度,如圖十七所示,由示波器進行頻率調整精度驗證,
經由實測,得知頻率調整精度為≦20Hz,如圖十八所示。
(4) 諧振頻率自動追蹤軟體模組與電路硬體模組整合
完成諧振頻率自動追蹤軟體模組,如圖十九所示,透過溫度感測擷取焊槍之溫度訊號,如圖
二十所示,透過溫度感測電路傳到30F4011數位訊號處理器,進行溫度與追頻演算程式判讀與
測試,並完成諧振頻率自動追蹤軟體模組與電路硬體模組整合,進行追頻計算,透過實測得知,
自動追蹤負載諧振頻率最大範圍可達40kHz,每5℃溫度偵測諧振頻率1次。
(5)300kHz 逆變器實測
為測試300kHz逆變器之可行性,本文已發展雛形系統進行實驗。測試系統諧振頻率介於
240kHz~360kHz間,負載功率1kW,測試進行時會隨著負載溫度變動對控制波形占空比進行
調變,由於當控制波形占空比小於20%時負載將充滿5次以上的諧波,可能對迴授系統造成嚴
重干擾,故溫度控制時對波形占空比控制範圍為20%~100%。
為驗證溫度控制功能,本文使用多功能桌上型電表搭配k-type 溫度線量測負載溫度,與
本文溫度量測系統之溫度作圖,分別設定目標溫度為100℃、120℃、160℃,實驗結果,如圖
二十一所示,可以看到溫度控制時,溫度震盪範圍不超過5℃,說明溫度控制之可行性。
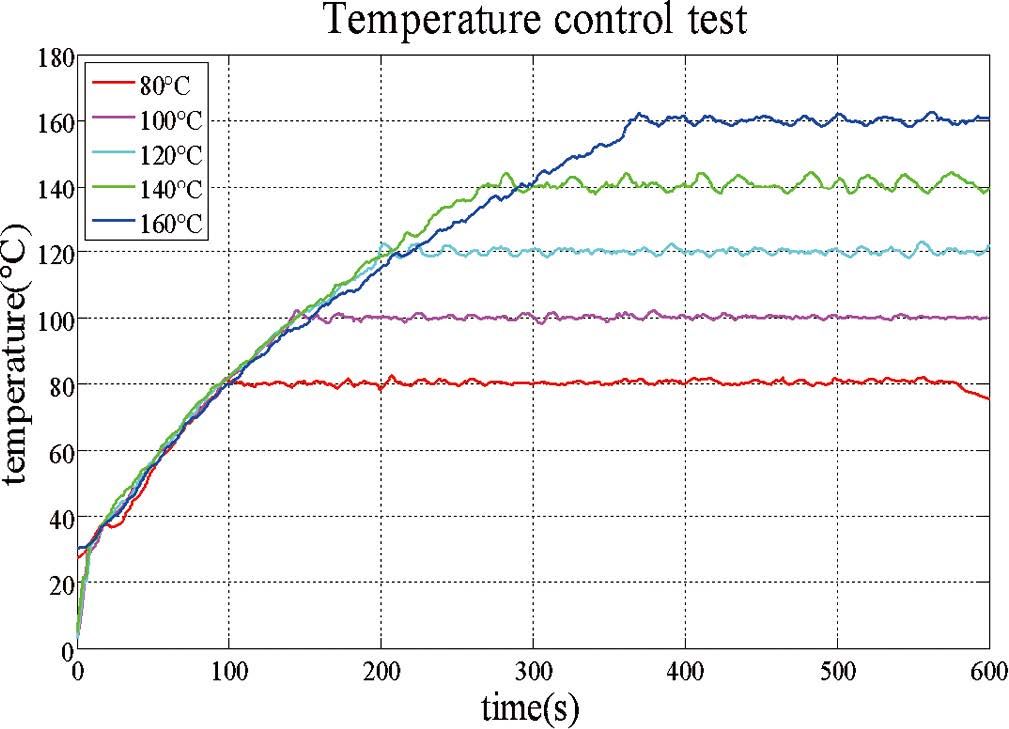
圖二十一、溫度控制實驗結果
(6) 電能轉換效率測試
進行感應加熱諧振頻率自動掃描追蹤模組整合感應加熱機台測試,如圖二十二所示,於測試
頻率自動掃描追蹤模組,首先使用LCR量測儀進行模具線圈負載搭配電感之量測,取得負載電感
值,如圖二十三所示,並以感應加熱諧振頻率自動掃描調變模組整合感應加熱機台測試,並進行
15.4kHz~40.1kHz之頻率調變測試,取得最佳諧振頻率為15.4kHz,輸入功率使用功率測量計
測試,輸出功率使用示波器測試,經由實測電能轉換效率可達91.9百分比,如圖二十四所示。
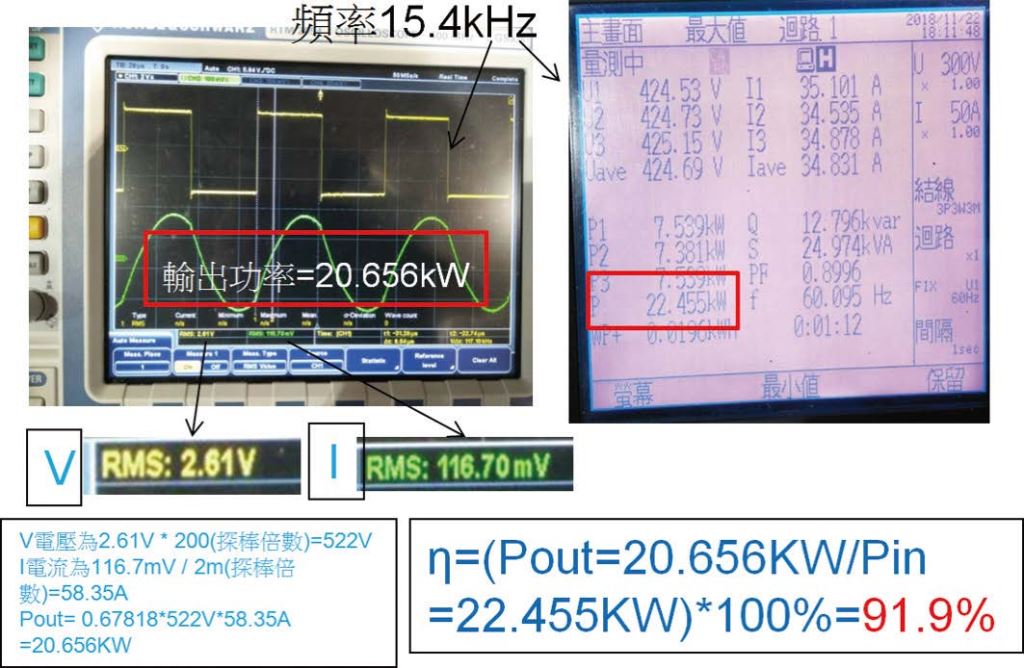
圖二十四、電能轉換效率實測
▋ 結論
於本精機中心,主要開發用於塑橡膠成形製程之感應加熱技術,開發追頻式電源模組電路
板,模組內部電路包含有相位偵測電路、訊號雜訊濾波電路、放大器電路與數位訊號處理電路,
經實際量測結果顯示(1)頻率相位偵測電路之精度≦1度。(2)頻率調整精度為≦20Hz。(3)電能
轉換效率可達91.9%。技術導入塑橡膠設備製造業者,及感應加熱電源主機業者,可提升其零組
件自主性及技術層次主機售價10%,並可衍生應用至壓出、熔接等產業,並可達到節省能源之
目的。針對300kHz感應加熱驅動控制電路,操作頻率達300kHz,在驅動、隔離電路的設計上
必須下更多功夫,在此一頻率下,絕大多數電路設計會面臨光耦合隔離驅動器頻寬不足、霍爾元
件頻寬不足、變壓器鐵芯材質頻寬不足、類比電流保護電路速度不夠快等問題。為克服上述問題
外,本文藉由純數位架構,以dsPIC數位訊號處理晶片為核心,同時具備可程式電流保護、通訊、
PWM、相位檢測功能,甚至不需要前級降壓轉換器輔助便能控制功率大小。由於沒有類比IC的
匹配需求,在量產上除了免除製板後須逐一校準的需要,壓低生產成本。另外純數位的設計流程
對於產品的設計時程將更短,單晶片的程式加密功能,有助於降低在商品化後被抄襲、複製的可
能性。發展高頻之感應加熱技術,有助於增加我國產業節能減炭之節能效益。
▋ 謝誌
本研究計畫承蒙經濟部能源署提供經費補助(計畫編號113-E0204),特此致謝。
▋ 參考文獻
- H.Sarnago, L.Óscar, andJ. M.Burdío, “A Comparative Evaluation of SiC Power Devices for High-Performance
Domestic Induction Heating,” IEEE Transactions on Industrial Electronics , vol. 62, no. 8, pp. 4795–4804,
2015.
- O.Jimenez, O.Lucia, I.Urriza, L. A.Barragan, andD.Navarro, “Power Measurement for Resonant Power
Converters Applied to Induction Heating Applications,” IEEE Transactions on Power Electronics , vol. 29, no.
12, pp. 6779–6788, 2014.
- M.Wesołowski, “Induction Heating of Thin Aluminum Layers During Depolymerization Process,” in
Progress in Applied Electrical Engineering (PAEE) , pp. 1–4 , 2017.
- K.Thepsatitsilp, W.Boonpeang, P.Saeung, N.Pukseesang, andC.Thongsopa, “Experiment and Design a
Suitable Induction Heating for Air Heat Exchanger Application,” in Electromagnetic Compatibility (APEMC),
2017 Asia-Pacific International Symposium on , pp. 161–163, 2017.
- T.Kute, A.Mahajan, andR. D. K.Barc, “Generation of Heat on Fuel Rod in Cosine Pattern by Using Induction
Heating,” Nascent Technologies Engineering (ICNTE), 2017 International Conferences, pp. 1–5, 2017.
- T.Matsuo andT.Okazaki, “A Basic Theory of Induction Heating for a Wind-Powered Thermal Energy
System,” Transactions on Magnetics , vol. 53, no. 11,pp.8110605, 2017.
- I. A.Makulov andA. E.Alitdinov, “The Equipment and Application Features of Induction Heating in Oil
and Gas Industry,” Industrial Engineering Applications and Manufacturing (ICIEAM), 2017 International
Conferences , pp. 1–4, 2017.
- I.Smolyanov, V.Frizen, K.Bolotin, andB.Ulrych, “Research of the Induction Heating Installation on Based
Autoclave,” in Computational Problems of Electrical Engineering (CPEE) , 2017 18th International
Conference on, pp. 1–4, 2017.
- Y.Peng, S.Wang, H.Cheng, andM.Chen, “Using Localized Induction Heating for Deep Ultraviolet Light-
Emitting Diodes,” IEEE Transactions on Components, Packaging and Manufacturing Technologies , vol. 6,
no. 9, pp. 1456–1461, 2016.
- S. A.Bychkov, F. E.Tarasov, V. E.Frizen, andI. A.Smolyanov, “Stamp Tool Induction Heating System,” in
Computational Problems of Electrical Engineering (CPEE), 2017 18th International Conference , pp. 1–4,
2017.
- T.Shijo, S.Kurachi, Y.Uchino, Y.Noda, H.Yamada, andT.Tanaka, “High-frequency Induction Heating for Small-
Foreign-Metal Particle Detection using 400 kHz SiC-MOSFETs Inverter,” in Energy Conversion Congress
and Exposition (ECCE) , pp. 5133–5138, 2017.
- A.Note, Keysight Technologies Practical Temperature Measurements.
- 陳秋君,“含加熱系統模具模溫之模擬與驗證”,私立中原大學機械工程研究所,碩士論文,2001。
- E. Horoszko, Krakớw, Polen, “Induction Heating of Flat Objects”, Arch. f. Elektvotechn., Bd.57, H 3, 1975.
- Davies E.J. and Simpson P.G.., “Induction Heating Handbook”, Mcgraw-Hill Book company Ltd.,
London(1995)
- E.J. Davies, “Conduction and Induction Heating”, IET Power Engineering Series1st Edition,1990.
- 林宥甯,“均勻模面加熱的嵌入式感應加熱單元之設計”,國立成功大學機械工程學系,碩士論文,2009。
- A. Hobson , “Physics 5th Editor”, Pearson College Div, 2009.
- M. H. Tavakoli, H. Karbaschi and F. Samavat, “Influence of workpiece height on the induction heating
process”, Mathematical and Computer Modelling 54 (2011) 50–58.
- M. Kranjc, A. Zupanic, D. Miklavcic and T. Jarm, “Numerical analysis and thermographic investigation of
induction heating“,International Journal of Heatand Mass Transfer 53(2010)3585–3591
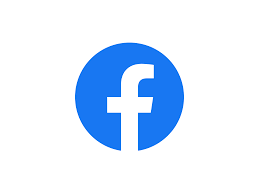 |
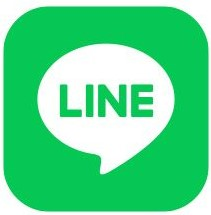 |