塑橡膠成形產業之工作站生產單元製程為反覆加熱與冷卻之週期性過程,於加熱和冷卻的時間,耗損了許多能量,另外絕大部分塑膠原料需經過除濕乾燥後才能投入生產,這都是塑橡膠成形製程耗能原因,對國內產業來說亦存在極大技術缺口。針對電磁乾燥設備技術比較傳統蜂巢式熱風烘料機之效益、具有節能效益,透過電磁燥機構設計,改善傳統熱風式間接加熱乾燥方式,可以節能55.8%,組合成連續式電磁乾燥機,補足塑橡膠成形設備製造業者間跨領域技術整合缺口,並落實產業實際應用,加速擴散本技術研發成果,協助突破塑橡膠成形產業節能技術門檻,進行產業化技術驗證,落實產業實際應用。
▋ 前言
為符合塑橡膠產業射出成形、押出成形、擠出成形與吹製成形前等塑料之乾燥需求,以及中上游塑橡膠設備、輔機製造業者之關鍵零組件技術亟需提升,以電磁乾燥設備機構關鍵零組件,取代傳統使用熱風、蜂巢式轉輪、分子篩或真空乾燥之技術,與傳統烘料製程比較,能提升能源使用效率。由於節能政策的興起,各國開始響應,目前國際有明確推動塑橡膠成形產業節能的國家,主要以歐盟「EUROMAP60.1」及中國大陸「塑料注塑成形機能耗檢測和等級評定」,為目前國際上規範塑橡膠產業節能的主要指標國家,主要於射出成形製程與設備能耗的測試規範,並訂定能耗等級關鍵標章,以鼓勵成形產業廠商精進節能製程及設備技術。相對於國外的節能規範上我國目前並無完整的推動政策,做為全球臺灣為全球第六大塑橡膠機械生產國及出口國,是十分急迫需要面對的議題,透過新技術之導入,推出低能耗成形塑橡膠烘料技術再創新。
▋ 電磁乾燥整機機構製作
本計畫為了使電磁乾燥機能更均勻的烘料,使用疊層式架構,搭配內部翻料葉片與分散模組,達到塑料乾燥更均勻的優點,電磁乾燥機機構分為整機機構( 出入料筒組裝、馬達傳動組裝、機架組裝與人機板金組裝等4種功能模組)與分散模組機構這2種機構之製作,各模組機構功能如下詳述:
1. 電磁乾燥整機組裝:
電磁乾燥機組裝使用兩乾燥筒疊層的模組化架構,使用者可依照烘料需求,增加或減少乾燥筒的數量,增加便利性,且透過3面透明壓克力窗之設計,能讓使用者知悉內部乾燥機運轉狀態,達到增加可視性的目的。
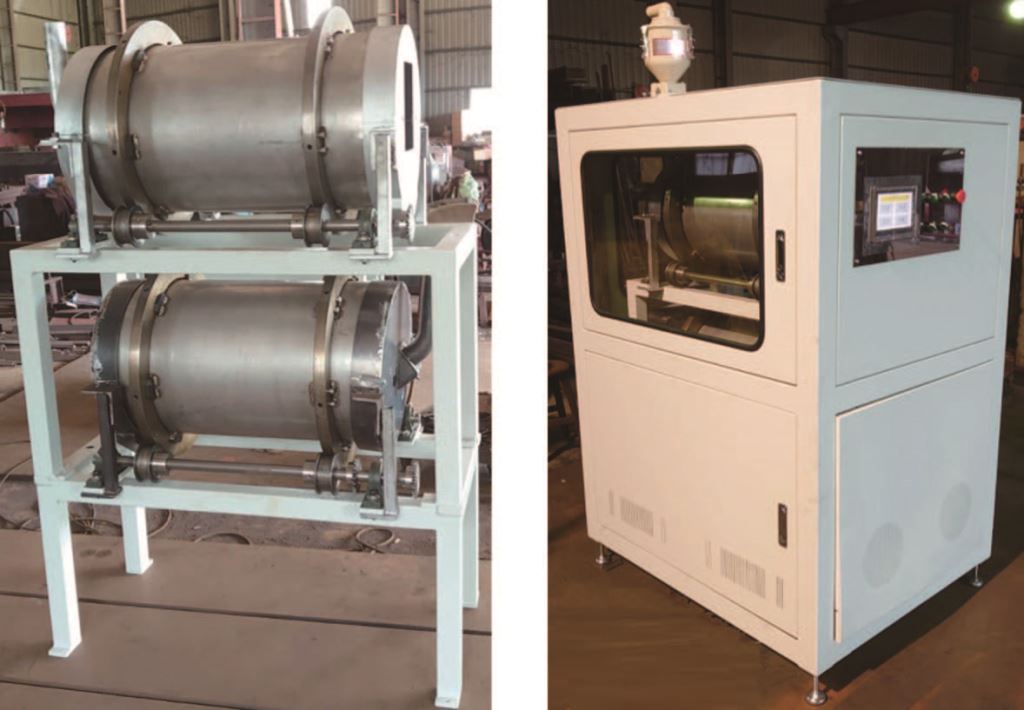
圖一、磁乾燥整機機構組裝
2. 分散模組組裝:
分散模組主要目的為增加電磁波分散的效果,達到塑料乾燥更均勻的目的;分散模組使用不鏽鋼,降低鏽蝕機率,步驟一: 使用雷切割將鋼板進行裁切,步驟二: 並將翻轉支架與螺旋葉片進行焊接。因翻轉支架設定為40度,可使電磁波於乾燥筒內進行反射,搭配乾燥筒金屬內壁與2顆磁控管位置配置,得到較均勻的電磁場,可使塑料能均勻的乾燥。

圖二、分散模組機構
3. 入出料筒組裝:
入料筒尺寸為直徑224mm,深度220mm,材質採用黑鐵,並加上烤漆防鏽,入料筒搭配極限開關,滿料時即可使極限開關動作,打開機構斜板直接下料;出料筒尺寸為300×400×150mm,材質採用黑鐵,整筒使用板金折彎工法製作,增加組裝之便利性。
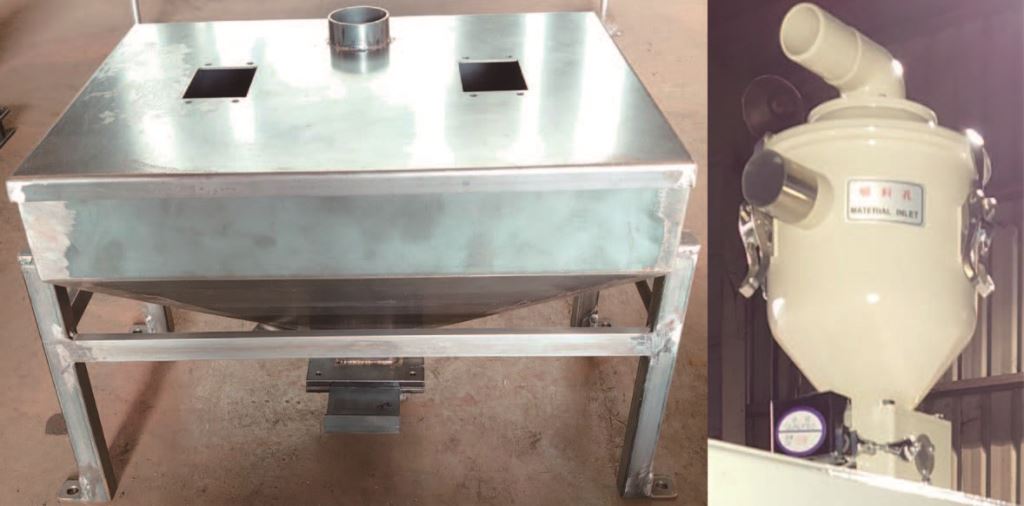
圖三、出入料筒組裝
4. 馬達傳動組裝:
電磁乾燥機構採用2條鍊條帶動4根傳動軸,馬達傳動機構採用模組化設計,達到易於組裝、拆卸與維修優點。
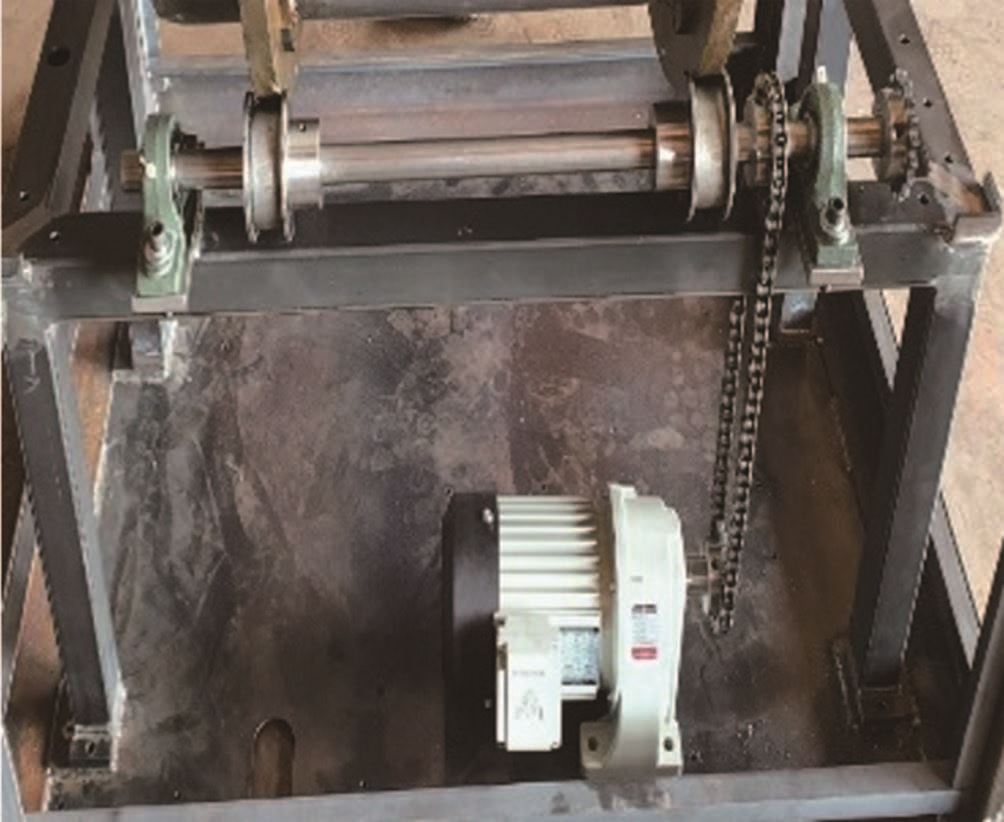
圖四、機架組裝
▋ 電磁乾燥控制硬體模組製作
一般電磁乾燥機均使用單顆驅動器功率約2.8kW驅動磁控管,因大功率磁控管價格昂貴,如需更換時費用較高。本計畫之電磁乾燥機,為符合乾燥筒腔體之大小配置,使用2~4顆功率900W驅動器,如需更換,可以單顆維修,不需要全部驅動器都更換,費用較低。本計畫開發電磁乾燥控制硬體模組,使用K-Type溫度感測器搭配溫控器進行電磁乾燥機溫度控制,並透過人機搭配PLC來進行電磁功率控制與溫度控制,達到2種參數之控制。各功能模組詳述如下:
1.電磁乾燥機硬體模組:
電磁乾燥機電控配盤採用鋁軌固定電控元件,主要電控元件包括:無熔絲電源開關、電磁接觸器、PLC、繼電器、變頻器等元件組成,搭配人機軟體之溫度與功率調控功能,完成電磁乾燥控制硬體模組之乾燥機溫度控制與磁控管功率控制2種功能控制,搭配線槽方便整理配線,並配置於乾燥機側邊之夾層,提高空間利用率,與一般配置於底板的乾燥機比,更提高了維修的方便性。
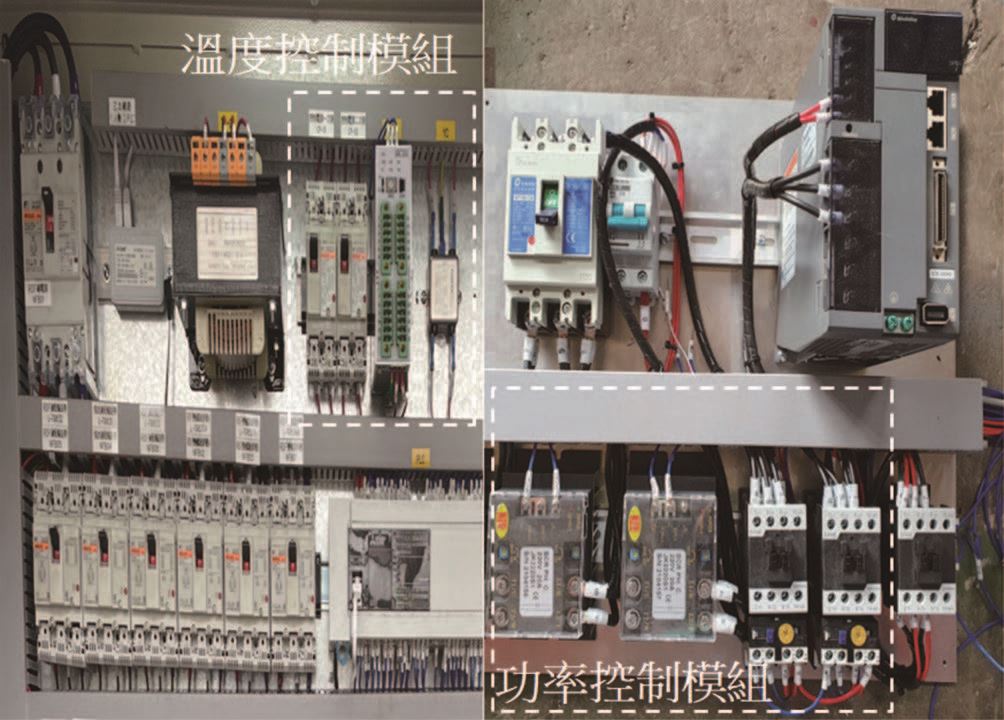
圖五、電磁乾燥機硬體模組
2. 功率控制模組:
以人機搭配PLC,進行電磁乾燥模組的功率調控,因應筒身設計符合乾燥筒內的配置,透過使用小功率(900W) 2~4 顆磁控管(型號:galanz m24fb-610a),透過磁控管產生連續震盪的高頻電磁波,由功率控制模組調整功率大小,搭配溫度控制與乾燥筒速度控制,達到控制塑料含水率的目的。
3. 溫度控制模組:
為提高電磁乾燥設備溫度控制穩定性,本計畫將K-TYPE 溫度感測器(型號:TS2)安裝於於2 乾燥筒之出料口,實際偵測塑料出料溫度,能避免溫度感測器於乾燥筒內,易受電磁波干擾的情形而使感測溫度受影響,此做法可提高溫度準確度。
▋ 電磁乾燥控制模組量測
本計畫電磁乾燥機,建置電磁乾燥控制模組,目的為了確保電磁乾燥設備之乾燥功能符合高含水率塑料之烘料需求,針對電磁乾燥控制模組進行量測,包括:人機介面功能測試、功率控制介面功能測試、溫度控制介面功能測試等,待單機功能測試後,後續進行實際烘料測試。
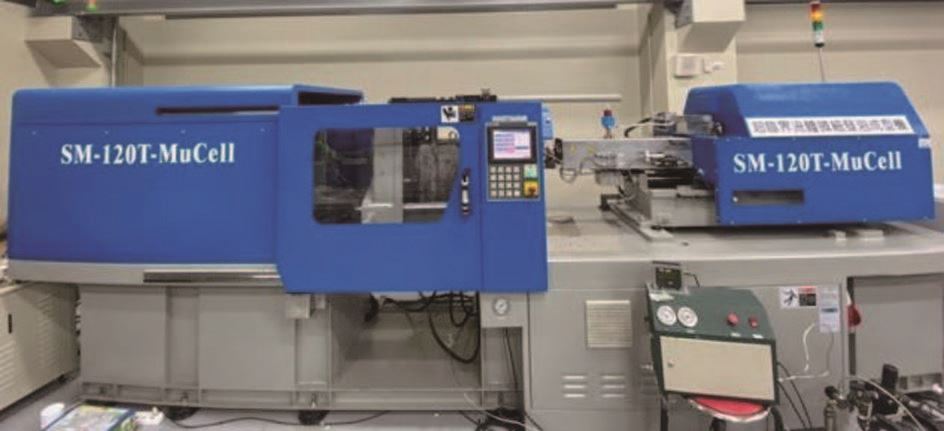
圖六、電磁乾燥控制模組測試
1. 電磁乾燥人機介面功能:
設計電磁乾燥人機,其目的為了提高使用者之操作便利性,電磁乾燥人機介面首頁,包括了:溫度設定、功率設定、配方管理與烘料演算法等,並加入了手動模式與自動模式,手動模式能依照使用者自由設定不同之溫度與功率,而自動模式則是由人機判斷目前之烘料桶溫度,來設定電磁烘料之功率。
2. 電磁乾燥功率介面功能:
本計畫需要調整電磁乾燥功率,其目的為依照不同的塑料調整不同的烘料時間和功率,達到不同的含水率,並依照使用者的烘料需求,自行設定手動加熱與解除。
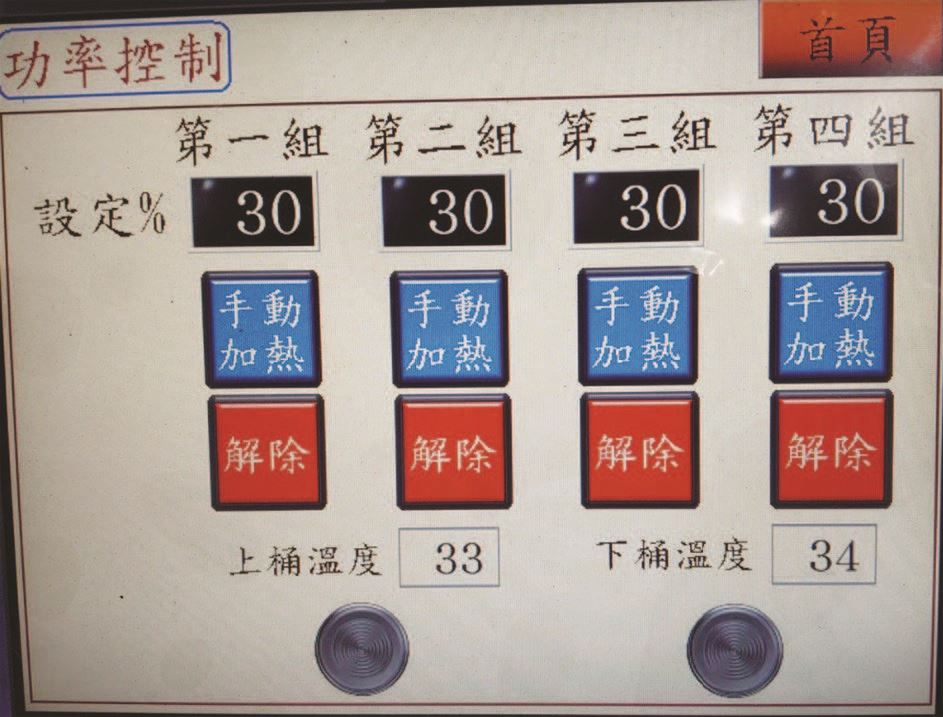
圖七、電磁乾燥功率控制介面
3. 電磁乾燥溫度介面功能:
電磁乾燥介面功能,其目的為讓使用者能得知目前乾燥筒的即時溫度,透過K-Type 溫度感測器,將溫度透過RS-485 通訊與人機進行連結,並顯示於人機螢幕上,使用者可以透過溫度設定,設定不同的溫度,可用於不同塑料之烘乾,增加使用烘乾塑料之寬容度。
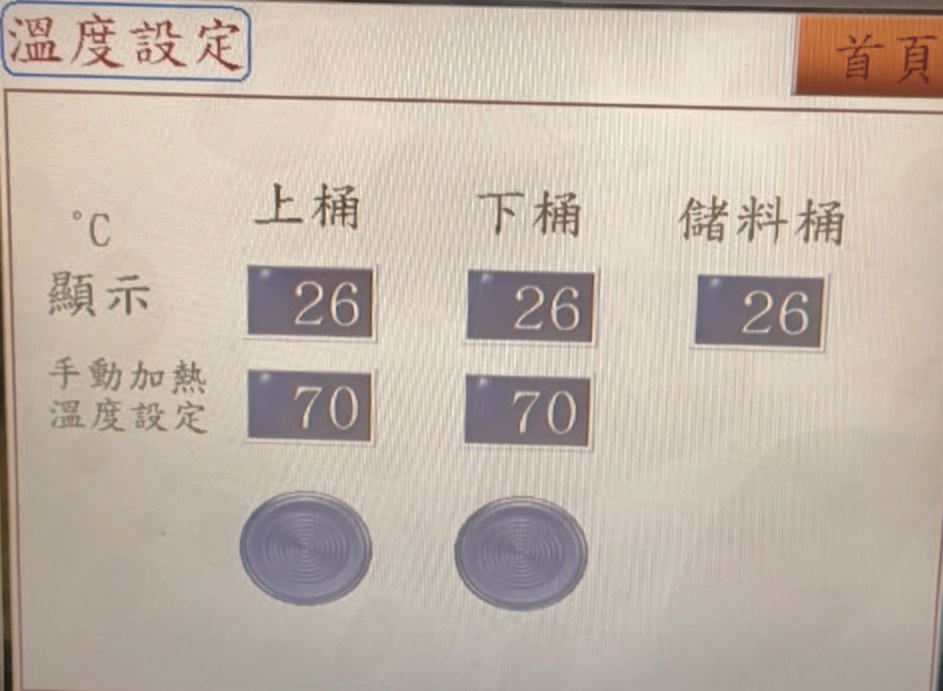
圖八、電磁乾燥溫度控制介面
▋ 低溫電磁乾燥機構與電控整合
完成低溫電磁乾燥機構電控整合測試與傳統蜂巢式乾燥機與電磁乾燥機烘乾時間比較,藉由曲線擬合所構成的演算模型,估算不同含水率時,所需要的乾燥參數,可降低操作者之調機時間,降低專業依賴度,並提高調機效率,整合電控後,進行電磁乾燥機與蜂巢式熱風乾燥機之烘乾時間比較,實驗結果為電磁乾燥機比蜂巢式熱風乾燥機縮短52.9% 之烘料時間。為解決目傳統蜂巢式熱風烘料機的缺點,如: 需長時間烘料、耗能高、烘烤溫度不均勻等缺點。因此本研究先針對烘料時間是否能縮短,先做實測驗證,避免當烘料時間過長時,導致塑料於射出時造成產品黃化等瑕疵,以確保塑料於短時間內達到製程含水率,避免塑料因長時間烘料導致物性改變,且提高產品之產能與節省能耗。
量測步驟:
Step1: 使用PC-110 塑料進行測試,搭配計時器與METTLER-TOLEDO 型號為3169-20 之含水率檢測儀進行電磁乾燥設備與傳統蜂巢式熱風烘料機之烘料時間實驗。
Step2: 使用尼龍(PC-110) 30kg 塑料,每10 分鐘取樣一次,並使用含水率計檢測數據與時間並記錄下來。
Step3: 電磁乾燥設備將與蜂巢式傳統乾燥機時間比較,比較含水率達到100ppm 之乾燥製程要求所需的時間。
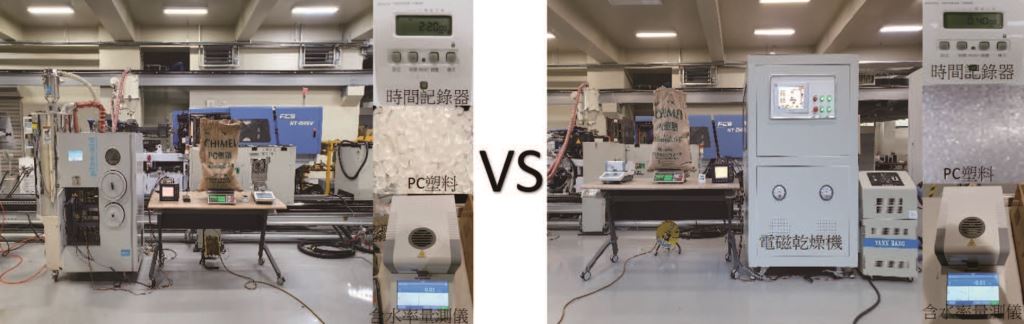
圖九、傳統(蜂巢式)VS 電磁烘料機烘料時間實驗架設
實驗測試結果:
PC-110 塑料由含水率測試儀測定的初始含水率數值為1400ppm,初始含水率數值測定後,將塑料分別倒入「傳統蜂巢式熱風乾燥機」與「電磁乾燥機」中,塑料由1400ppm 乾燥至100ppm,並且每10 分鐘取樣一次,使用含水率計檢測塑料含水率數據,並將塑料含水率達100ppm 之時間並記錄下來,經由實測結果得知,電磁乾燥機將PC-110 乾燥至100ppm 所花之時間花費80 分鐘,比傳統蜂巢式熱風乾燥機之時間為170 分鐘,時間縮短52.9%,實驗結果證明,本計畫所開發之電磁乾燥機構確實可以有效提高烘乾效率,降低烘料時間,提高產能。
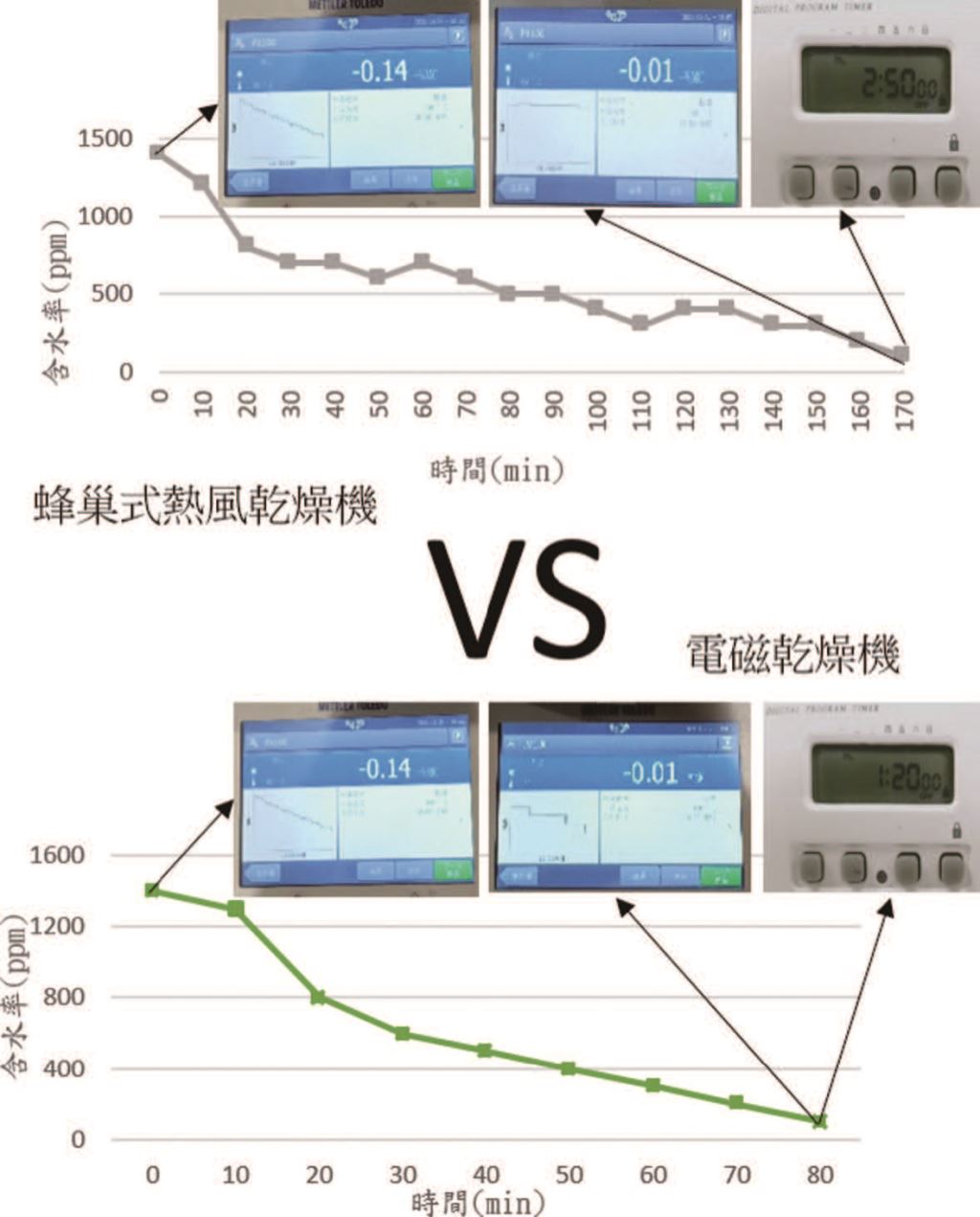
圖十、傳統蜂巢式熱風乾燥機VS 電磁乾燥機烘料時間實驗
▋ 電磁乾燥機烘料節能量測試
改善傳統蜂巢式熱風乾燥機烘料之方式,透過磁控管之電磁波,進行塑膠材料的烘乾,分為單段與多段(兩段)烘乾製程,透過功率檢測儀量測能耗,完成電磁乾燥設備烘料節能量測試,主要係透過比較傳統蜂巢式熱風乾燥機與電磁乾燥機於烘料與節能上的差異,並針對二者所的能耗進行實驗比對與測試。
量測步驟:
Step1: 使用METTLER-TOLEDO 含水率檢測儀型號為HC103 進行塑料含水率量測、HIOKI 功率檢測儀型號為3169-20 進行節能量量測。
Step2: 使用尼龍(PC) 30kg 塑料,每4 分鐘取樣一次,並使用含水率計檢測數據並記錄下來,同時每10 分鐘一次由功率檢測儀記錄累計功率值。
Step3: 電磁乾燥機將與蜂巢式熱風傳統乾燥機時間比較,比較含水率達到100ppm 之乾燥製程要求所需的能耗。
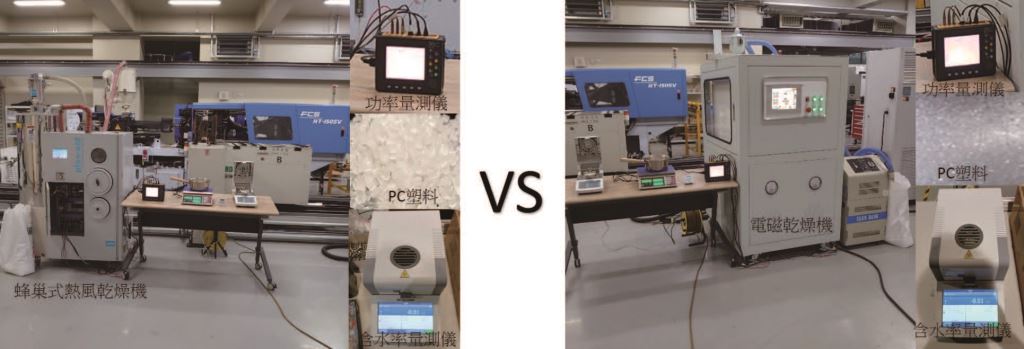
圖十一、傳統(蜂巢式)VS 電磁乾燥設備烘料能耗實驗
實驗結果:
電磁乾燥機部分,將塑料由1400ppm 乾燥至100ppm,耗能6289.4Wh,比傳統(蜂巢式)耗能14233Wh,節能量55.8%。若於乾燥設備再導入烘料配方控制與參數演算法,能使烘料參數快速達到最佳化,且比傳統烘料設備更節能,故可以為產業界達到節省能源成本之目的。
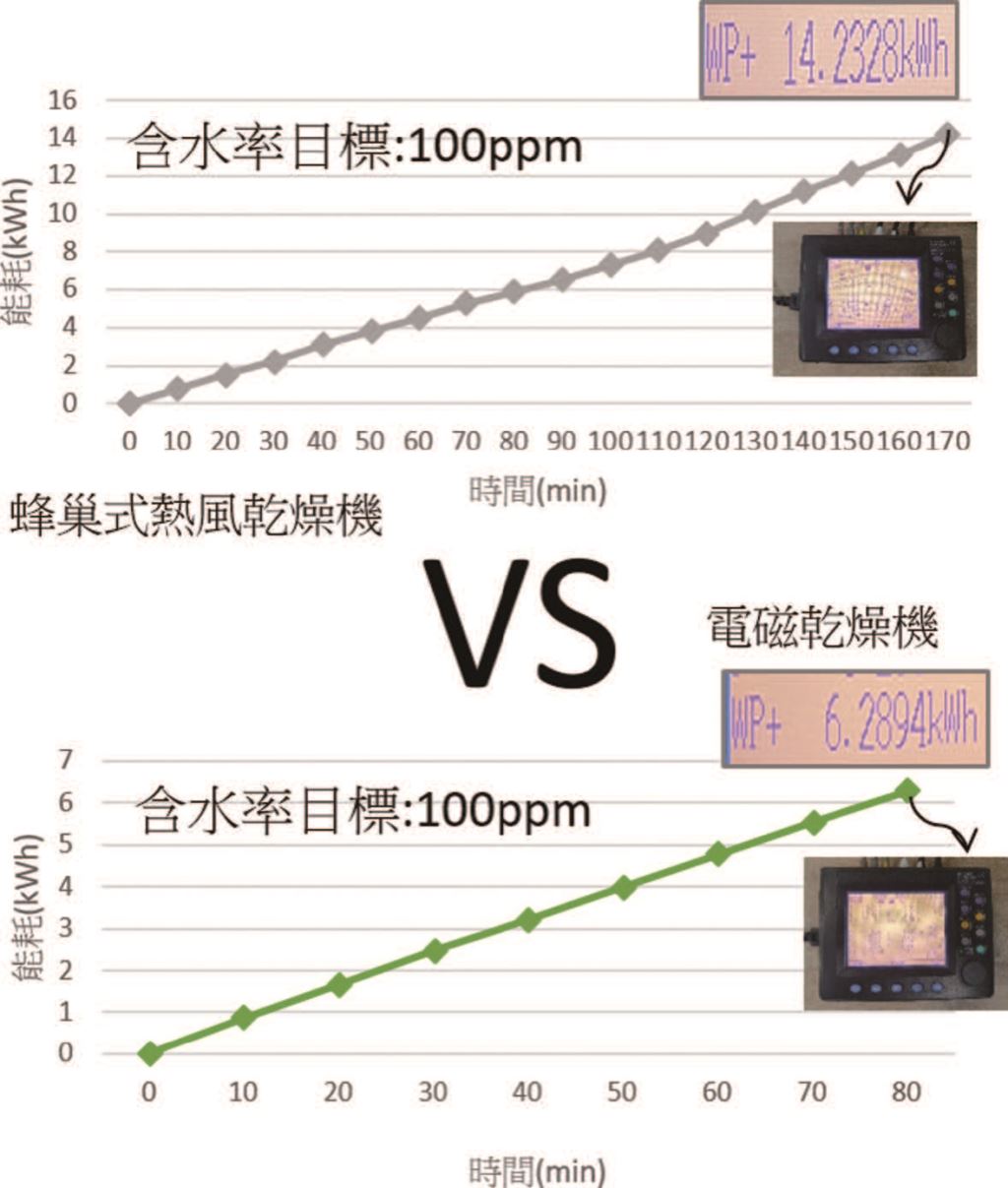
圖十二、蜂巢式熱風烘料機 VS 電磁乾燥機功率消耗圖
▋ 結論
近年來功能性塑膠製品的應用與日俱增,塑橡膠成形產業之工作站生產單元製程為反覆加熱與冷卻的週期性過程,大部分塑膠原料需經過除濕乾燥後才能投入生產,這都是塑橡膠成形製程能耗較大的原因,本中心開發電磁乾燥技術,改善傳統熱風式塑料間接加熱乾燥方法,時間長、能耗高的問題,利用電磁波特性直接對於塑料中的水分子進行加熱乾燥,提升能源使用效率,烘料時間和能耗將可大幅改善。本中心投入原料除濕乾燥之技術項目進行開發,對於乾燥機節能技術上,聚焦電磁乾燥技術,透過電磁乾燥模組直接加熱方式同時針對塑料內水分進行乾燥,改善原本熱風式間接加熱乾燥方式,提升能源使用效率,與傳統烘料法比較,可以節能55.8%,然而隨著全球環保意識抬頭,上游品牌公司(例如:Apple、Samsung、ASUS)對於環境責任越來越重視,紛紛要求產業鏈下游供應商採用節能與環保的綠色製造技術,面對新的產業環境,綠色製造科技的發展與導入,做到塑橡膠整廠工作站生產單元製造過程節能、節料、精簡製程、降低不良率、提高加工速度乃至人力都是當前國內塑橡膠成形產業發展迫切需解決之問題。
▋ 謝誌
本研究計畫承蒙經濟部能源局提供經費補助(計畫編號112-E0204),特此致謝。
- Bruce F. Taylor, ” Apparatus and method for inductive heating a workpiece using an interposed thermal insulating layer”, US20080136066, 2008-6-12.
- Hotwise, ” Induction heating - Injection Molding Machine ”, 2008, form http://hotwise.net/msg.php?id=7
- Guilong Wang, ”Research of thermal response simulation and mold structure optimization for rapid heat cycle molding processes, respectively with steam heating and electrical heating.” , MATERIAL AND DESIGN, 2010.
- A.C. Liou, R.H. Chen, “Injection molding of polymer micro- and sub-micron structures with high-aspectratios”, International Journal of Advanced Manufacturing Technology,Vol. 28, No. 11-12, pp. 1097-1103, 2006.
- Donggang Yao and Byung Kim, “Development of Rapid Heating and Cooling Systems for Using Injection Molding Applications”, Polymer Engineering and Science,Vol. 42, No. 12, pp. 2471-2481, 2002.
- D. Yao and B. Kim, “Development of Rapid Heating and CoolingSystem for Injection Molding Applications”, Polymer Engineeringand Science, Vol. 42, No. 12, pp. 2471-2481, 2001.
- 行政院,“國家節能減碳總計畫”,民國99年。
- 史勇春,李捷,李選友,吳茂剛,趙改菊,尹鳳交,“過熱蒸汽乾燥技術的研究進展”,乾燥技術與設備,第10卷,第1期,民國101年。
- J. Lamoree, D. Muller, P. Vinett, W. Jones, and M. Samotyi, “Voltage Sag Analysis Case Studies,” IEEE Transactions on Industrial Applications, Vol. 30, No. 4, pp. 1083-1089, Jul./Aug. 1994.
- R. D. Henderson and P. J. Rose, “Harmonics: The Effects on Power Quality and Transformer,”IEEE Transactions on Industry Application, Vol. 30, No. 3, pp. 528-532, May-June 1994.
- 江榮城,“電力品質實務( 一)”,全華科技圖書股份有限公司,民國90年。
- D. M. Vilathgamuwa, A. A. D. R. Perera, and S. S. Choi, “Performance Improvement of the Dynamic Voltage Restorer With Closed-Loop Load Voltage and Current-Mode Control,” IEEE Transactions on Industrial Applications, Vol. 17, No. 5, pp. 824-834, September 2002.
- S. S. Choi, B. H. Li, and D. M. Vilathgamuwa, “Dynamic Voltage Restoration with Minimum Energy Injection,” IEEE Transactions on Power Systems, Vol. 15, No. 1, pp. 51-57, February 2000.
- D. M. Vilathgamuwa, H. M. Wijekoon, and S. S. Choi, “Interline Dynamic Voltage Restorer: An Economical Way to Improve Interline Power Quality,” IEE Proceedings-Generation, Transmission and Distribution, Vol.150, No. 5, pp. 513-520, September 2003.
- N. H. Woodley, L. Morgan, and A. Sundaram,“Experience with an Inverter-Based Dynamic Voltage Restorer,”IEEE Transactions on Power Delivery, Vol. 14, No. 3, pp. 1181-1186, July 1999.
- S. S. Choi, B. H. Li, and D. M. Vilathgamuwa, “Dynamic Voltage Restoration with Minimum Energy Injection,” IEEE Transactions on Power Systems, Vol. 15, No. 1, pp. 51-57, February 2000.
- D. M. Vilathgamuwa, H. M. Wijekoon, and S. S. Choi, “Interline Dynamic Voltage Restorer: An Economical Way to Improve Interline Power Quality,” IEE Proceedings-Generation, Transmission and Distribution, Vol.150, No. 5, pp. 513-520, September 2003.
- N. H. Woodley, L. Morgan, and A. Sundaram,“Experience with an Inverter-Based Dynamic Voltage Restorer,”IEEE Transactions on Power Delivery, Vol. 14, No. 3, pp. 1181-1186, July 1999.
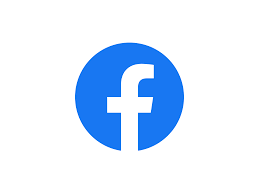 |
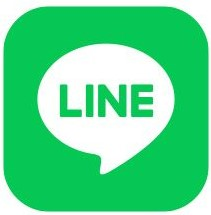 |